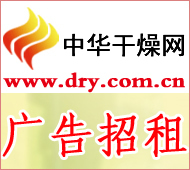
The Yima Gasification Plant of Henan Coal Gasification Group learned that the phenol-containing ammonia water that has plagued them for a long time was used to solve desulfurization problems and was cracked at one stroke. After the joint efforts of Luoyang City Tianyu Environmental Engineering Co., Ltd. and Yima Gasification Plant, the adoption of resin to adsorb phenolic substances completely eliminated the company's annoyance.
The long-term operation shows that the phenol waste ammonia produced by the Yima Gasification Plant at present has played a super value role and was successfully used for the desulfurization of boiler flue gas, achieving the “multiple birds with one stone†effect: not only on-site digestion The waste ammonia water also effectively reduced the sulfur dioxide emissions in the coal chemical production process. The by-product ammonium sulfate can be used as a compound fertilizer raw material with low cost and good efficiency. According to environmental experts, the technology is unique in the country.
The problem encountered by Yima Gasification Plant is widespread in many coal chemical companies. In the field of coal chemical industry, the first process is coal gas. During this process, some of the nitrogen in the coal will be converted into ammonia, forming by-product ammonia. These ammonia waters contain phenolic substances. If they are sold as products, the phenol content must be greatly reduced, and ammonia should be purified and recovered. However, the recovery of production is not large, the price is not high, the investment is very large, the cost and efficiency upside down, the company simply does not have enthusiasm, so most of them tend to be indigestion of phenol-containing ammonia on the spot. On the other hand, the flue gas produced by coal chemical boilers must be qualified after desulfurization, which requires ammonia. It is understood that ammonia desulfurization is the best in all current desulfurization methods. If waste ammonia is used for desulfurization, it is undoubtedly the best way out.
Yima Gasification Plant was once pinched by phenols during the practice of ammonia desulfurization. In the use of phenol ammonia, although the desulfurization effect is good, but the side effects are also great: ammonia for the formation of ammonium sulfite in the desulfurization process, the latter need to be oxidized to play a role, but due to the easy oxidation of phenol and oil characteristics, not only with Ammonium sulphate competes for oxygen, and can easily accumulate locally at the gas-liquid interface of the oxidation reaction interface, thereby preventing the ammonium sulphite from being sufficiently contacted with oxygen, resulting in that ammonium sulphite is difficult to be effectively oxidized to ammonium sulfate and ammonium sulphate, a byproduct, is recycled to form a dilemma. Even if it can be recycled in small amounts, purity is difficult to meet the national standard.
So, how can we digest both phenol and ammonia water on the spot so that “waste†can take on the responsibility of desulphurization and environmental protection, and the ammonium sulfate by-product can be recovered smoothly and meet high quality requirements?
Luoyang Tianyu company after research, that the technical bottleneck is to remove phenol from the desulfurization solution before the ammonium sulfite oxidation, but also cost-effective to pay, but this point there is no domestic successful industrialization examples for reference. Luoyang Tianyu has a large number of self-developed environmental protection patented technologies, and the wet ammonia process desulfurization technology suitable for national conditions has produced good results in many domestic chemical companies. Based on the accumulation of technology, Tianyu eventually developed a technology that uses resin adsorption to remove phenol from the desulfurization solution.
This technology allows the phenol to be separated from the desulfurization solution and the phenol content in the desulfurization solution is reduced to less than 20 mg/l. Previously, this indicator was generally only able to be achieved using foreign technology. However, long-term foreign technological processes, high energy consumption, and high consumption of extractant are not suitable for China's coal chemical industry conditions. The use of domestic technology to produce the extractant species and purity is limited, the extraction of ammonia in phenol is difficult to achieve the desired level, the phenol content is generally exceeded, and some plants recovery of ammonia in the phenol content even up to thousands of milligrams per liter. Tianyu's technology can not only achieve low-cost operation, but also reduce the content of phenol, and ultimately enable the ammonium sulfite to complete the oxidation, so that the by-product ammonium sulfate recovery rate increased to 95% or more, product quality meets the requirements of GB535-1995 superior products standard. At the same time, the resin used for dephenolization can also be regenerated, and the removed phenol can be recovered in the phenol recovery section of the original plant.
With this resin dephenolization technology, the waste ammonia produced in the domestic coal chemical production process can play a role in desulfurization. The application results show that the desulfurization effect is satisfactory, and the sulfur dioxide content in the boiler flue gas is not more than 100 mg/standard cubic meter, which provides a low-cost, high-efficiency utilization of phenol ammonia water desulfurization for coal chemical companies.
Custom Metal Stamping Services
Jiantong Hardware offers custom Metal Stamping services from prototype through production quantities. We run stamping in a variety of metals include Mild steel, stainless steel, aluminum, brass, copper and metal alloy. Thickness we`re able to proceed ups to 0.315"(8mm) thick, but our specialty is .008"(2.0mm)-.236"(6.0mm) thick with high-volume and tight tolerance. Our presses have full feed lines and are die sensor protection ready. We run nearly 60 million stampings per year at a 95% on time delivery rate.
Our mould type include progressive and single hit dies, presses capabilities range from 8 tons to 400tons. We promise all our products are fully inspected using vision systems, optical comparators, CMM equipment and functional gauges before shipment. Industries we have served include aerospace, medical, automotive, home appliance and electronics.
Other advantages:
· In-house tooling, gauge and fixture building
· Free samples will be offered on request
· We support prototype and lower MOQ
· 4 years of gold supplier in alibaba provides full guarantee of trade transactions
· Inspection processes capable of first article, PPAP, collecting CPK data, lot controlling and functional checks
With Wire EDM, CNC lathe, CNC machining, Grinding and milling, we can be a single source for your assembly and sub-assembly needs. Reach us today and save your money !
Stamping Parts,Precision Metal Stamping,Custom Stamping Parts,Aluminum Stamping
Nanpi Jian Tong Hardware Manufacturing Co., Ltd. , http://www.jiantongstamping.com