The size of the cold storage should be designed based on the maximum amount of agricultural products to be stored throughout the year. This capacity is calculated based on the volume required to store the product in the cold storage, plus the distance between the rows, the space between the stack and the walls, the ceiling, and the gap between the packages. After determining the capacity, determine the length and height of the cold storage. Cold storage design must also consider necessary auxiliary buildings and facilities, such as workshops, packing and finishing rooms, tool warehouses and loading docks, so that the quality of cold storage can be guaranteed.
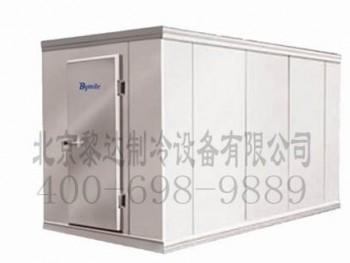
2. The selection and construction of insulation materials are very important to the quality of cold storage:
The selection of cold storage thermal insulation materials must be based on local conditions. It must have good thermal insulation performance and be economical and practical. Insulation materials are divided into several types. One is a plate processed into a fixed shape and specifications, and has a fixed length, width, and thickness. A plate of a corresponding specification can be selected according to the requirements of the installation of a cold storage body. Generally, high and medium temperature cold storage is selected 10 Thickness of the library plate, low temperature cold storage and freezing cold storage generally use 12 cm or 15 cm thick plate; the other can be sprayed with polyurethane foam, the material is sprayed directly to the built brick or concrete warehouse, after shaping Both moisture and heat insulation. Insulation plates include polyurethane, polyphenylene, and the like. Polyurethane is not water-absorbent and has good heat insulation, but its cost is high. Poly-phenyllate has strong water absorption and poor heat insulation, but its cost is low. The structure of the modern cold storage is being developed in a forward direction. It has been built into a warehouse structure that includes a moisture-proof layer and a thermal insulation layer. The advantage of this is that the construction is convenient, rapid, and portable, but the cost is relatively high.
3. The choice of refrigeration system is most important for the quality of cold storage:
The choice of cold storage refrigeration system is mainly the choice of compressor and evaporator. The refrigeration system is the core of the cold storage. It is mainly composed of a compression system, a condensing system, an evaporation system, and a regulating valve. In addition, there are accessories such as fans, ducts, and meters. The entire refrigeration system is a sealed circulation loop. The refrigerant circulates in the sealing system, and the supply quantity and the number of times of entering the evaporator are controlled as required to obtain a suitable low temperature condition. The compressor is the heart of the refrigeration system, which promotes the circulation of the refrigerant in the system. The function of the condenser is to eliminate the heat in the compressed gaseous refrigerant and condense it into a liquid refrigerant. The cooling methods of the condenser include air cooling, water cooling, and air-water combination. The air cooling is limited to small refrigerators. Application in refrigeration equipment. The role of the evaporator is to provide cold storage to the cold storage. The evaporator is installed in the cold storage. The blower blows the cooled air to various parts of the warehouse. The common cold storage is used to connect the evaporator and extend the air supply distance. The temperature dropped more evenly.
Pre-painted steel coil, also referred to as Color Steel Coil, is based on hot-dipped Galvanized Steel Sheet. Talk over with factory pre painted zinc coated metallic, in which the metallic is painted before forming, in preference to publish portray which happens after forming.Its major characteristics include top colorability, formability and corrosion resistance, as well as the mechanical electricity and processability of steel plate.Clients can recommend necessities to producers in keeping with their own specs of prepainted steel coil, as a way to perform manufacturing.
The color coating production process is divided into substrate pretreatment, chemical conversion film (non-organic metal coating), organic non-metal coating, and some production lines have post-coating processes. Organic coatings are divided into primers and topcoats. The requirements for primers are not high and can be painted smoothly. However, for the sake of production safety, companies generally use color reverse coating methods for primers and topcoats. Post-coating process: The post-coating process includes printing, embossing, peelable protective film, lamination, etc., which increase the decoration and protection performance of the color coated steel sheet.
Pre-Painted Steel Coil,Pre Painted Steel Sheet,Color Painted Steel Coil,Prepainted Galvanized Steel Coil,Color Steel Coil
Jinan Hengming Steel Co., Ltd , https://www.jnhengmingsteel.com