Introduction: Machinery needs long-term maintenance and care to operate, mechanical sealant failure causes: rubber parts of the old rubber parts of aging, deformation, mainly in the water pump hardening, deformation. Mechanical sealant failure performance of the phenomenon of water temperature is too high, the medium dissolves rubber. In terms of appearance, the surface of the rubber piece is loose, rough, and loses its elasticity, thus causing the rubber to fail.
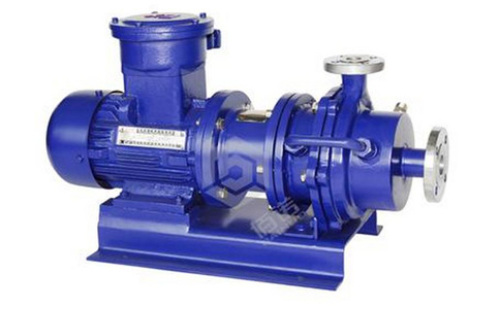
First, the mechanical seal failure performance on the part:
1, the failure of the seal face: wear, hot cracking, deformation, damage (especially non-metallic seal face).
2, spring failure: relaxation, fracture and corrosion.
3. Failure of auxiliary seals: Assembled failures include chip, crack, bump, curl and distortion; unassembled failures are deformed, hardened, broken, and deteriorated.
Mechanical seal failures appear as vibration, heat, wear, and eventually appear as media leaks.
Second, the leakage of mechanical seals may be the mechanical and static ring plane wear of the mechanical seal, resulting in the mechanical seal, wear and tear of the plane due to the following 9 aspects:
1, installed too tight
Observe the plane of the moving and stationary ring of the mechanical seal. If there is severe scorching, deep black marks on the plane, or hardened sealing rubber or loss of elasticity, this is due to the tightness of the installation.
Treatment method: Adjust the installation height. After the impeller is installed, pull the spring with a screwdriver. The spring has strong tension. After releasing, it is reset. There is a moving distance of 2-4 mm.
2, installed loose
Observation machine seal, stationary ring plane, its surface has a very thin layer of scale (can be wiped off), and the surface is basically no wear, which is caused by the loss of elasticity and poor assembly of the spring, or caused by the axial movement of the motor .
3, poor water quality particles
Due to the poor water quality, there are small particles and high content of hydrochloric acid in the medium, and grooves or ring grooves are formed on the plane or strain surface that forms the abrasive wear machine seal.
Treatment method:
Understand the liquid condition (with or without debris, etc.). Remove the pump and inspect and inspect the mechanical seal for damage. Improve water pressure or media and replace machine seals.
4, dry running damage caused by dry running
This phenomenon is more common in the bottom valve installation type inlet negative pressure, the inlet pipe has air, the pump cavity has air, after the pump is turned on, the friction of the machine seal produces high temperature during high-speed operation, can not be cooled, check the machine seal, spring tension Normally, the friction surface burns black and the rubber hardens and cracks.
Treatments: Drain the air in the duct and pump cavity or replace the mechanical seal.
5, cavitation
Cavitation is mainly caused by hot water pumps. Because the medium is hot water, the water temperature is too high to generate steam, and the vapor in the pipeline enters the high position in the pump chamber. This part of the vapor cannot be eliminated, resulting in water shortage operation and mechanical seal dry grinding failure.
Treatment method: Air bleed installed automatic exhaust valve, replace the machine seal.
6, assembly problems
It may not be installed when the pump cover is installed, resulting in that the shaft and the pump cover are not perpendicular to each other and the static and dynamic planes cannot be matched. The startup time is not long, causing unilateral wear and water seeping.
Treatment: Remove and reinstall, check the pump cover is installed.
7. The type selection is incorrect (the machine seal that is suitable for the use condition is not selected according to the use requirements, especially the use environment for conveying the corrosive liquid).
Inspection method: Learn more about pumping liquid composition, temperature, and corrosion. Remove the pump and inspect and inspect the mechanical seal for damage.
8. The eighth possibility of leakage of water at the mechanical seal is the poor machining accuracy, small size, roughness and journal corrosion of the motor shaft. The main reason is that the motor's journal (moving ring) processing size is small, or due to corrosive corrosion of the pump shaft dielectric, and due to a long time out, water as a medium, the electrode potential of the steel shaft and the casting impeller, pump cover is different , forming a galvanic reaction, causing journal corrosion. The phenomenon of manifestation is the spotted surface of corrosion.
Treatment method: The rusted surface is polished with sandpaper. After being wound with the raw material tape, it is placed in a moving ring for emergency treatment. The best method is to change the axis, or to restore the original shaft size after shaft inserting.
9. The second possibility of leakage of water at the mechanical seal is the failure of the mechanical sealant.
Reasons for the failure of the mechanical sealant: The aging and deformation of the old rubber parts of the rubber parts are mainly caused by hardening and deformation in the water pump. Mechanical sealant failure performance of the phenomenon of water temperature is too high, the medium dissolves rubber. In terms of appearance, the surface of the rubber piece is loose, rough, and loses its elasticity, thus causing the rubber to fail.
Treatment: Replace suitable rubber material.
Injection Tooling & Mold Design
Professional injection molding customized products for 20 years, to provide you with a reassuring customized experience, in order to ensure product quality, the company strictly follows the ISO9001:2015 quality management system for management, one-stop service for assembly and packaging, free design for large quantities, affordable prices, and high quality Guarantee is your trusted source manufacturer.
Fast quotation, medical, electronic, automotive, household mold injection molding customization. Professional injection molding customized products for 20 years, to provide you with a reassuring customized experience. With many years of industry production experience, we can process and order according to drawings and samples, source manufacturers, quality assurance, complete specifications, high-quality after-sales service, modern complete sets of production equipment and superb workforce, with an annual production capacity of nearly 1,000 tons. Liquid silicone vulcanization molding equipment, injection molding process, extrusion/extrusion.
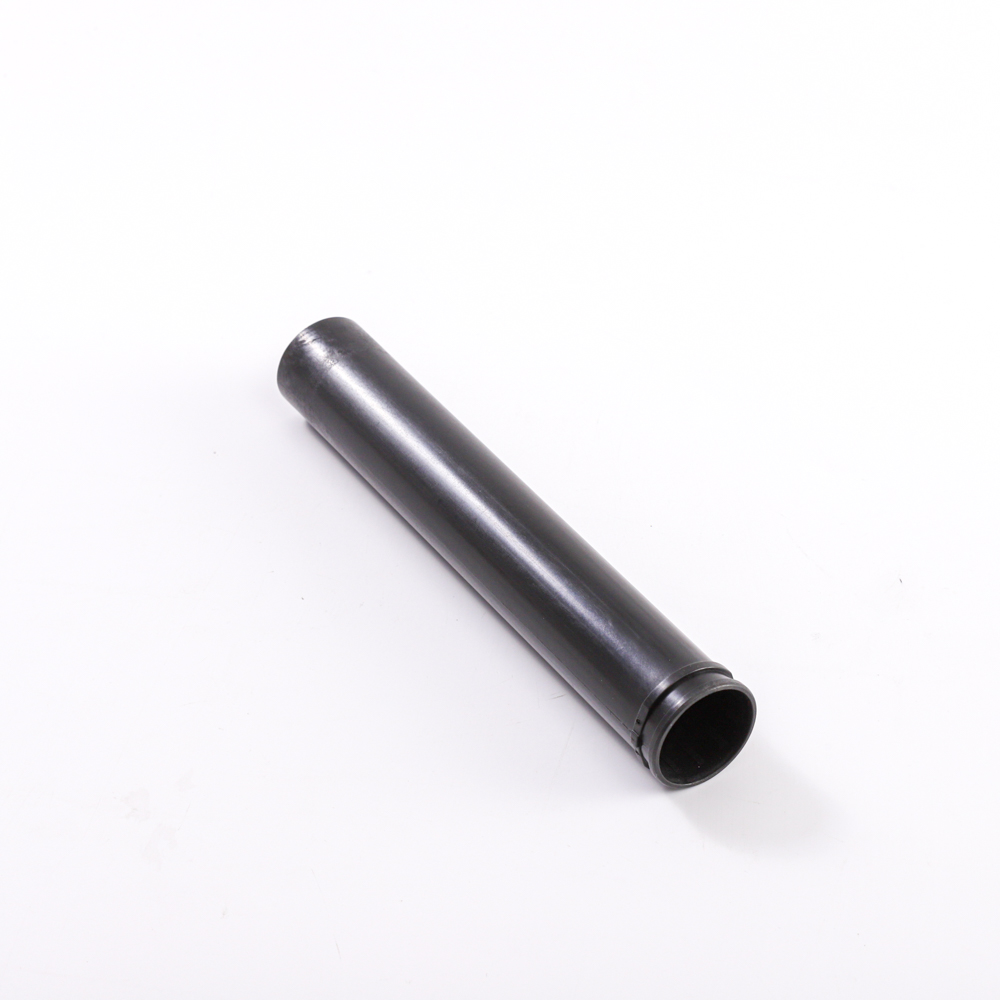
Injection Tooling & Mold Design,Injection Molding Tooling Design,3 Plate Injection Mold Design,Injection Molding Die Design
Suzhou Dongye Precision Molding Co.,Ltd. , https://www.dongyeinjectionmolding.com