1. Overview As a PC based upper control unit, the motion control card has greater flexibility and openness in the development process of the special machine system. Enables users to develop powerful motion control systems in the short term. Because of the above characteristics, professional motion control cards are not only widely used in the machine tool industry, but also are widely used in many small-scale special plane systems. This article will take Stepper Electromechanical Company MPC01 series motion control card as an example to introduce the application of single axis motion control card in CNC punch press feed system.
2. CNC Punch Motion Control System (1) System Actuator and Upper Controller:
In the single axis feeding system of CNC punch press, the no-load response time of the executing motor is required to be within 40-60ms. The response time of the stepping motor (usually about 200ms) can not meet the requirements of the rapid response of the system, so the system uses Panasonic AC servo motor MSMA750W and DMC301A as the implementation of the motor and the host controller.
The following is the wiring diagram of the motion control system circuit:
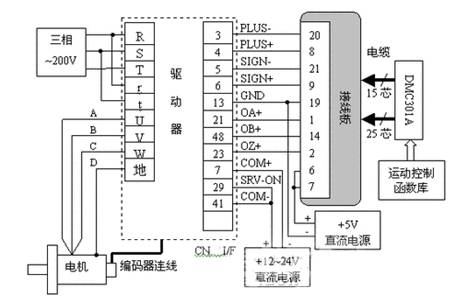
Wiring diagram of DMC301A and MINASA series
(2) System software control part This system software uses VB for programming. Because MPC01 motion control card is equipped with a powerful dynamic link library (DLL), users can quickly develop their own motion control system in the Windows system environment. And for Win's multi-task mechanism, MPC01 motion control card uses a virtual device driver (VXD) technology, which solves the real-time problem of the control system in the Win environment. When the program is initialized, using the declaration module (MPC01.BAS) to link the dynamic link library in the form of a header file, the user can call the motion control function of the board like calling the Windows internal function.
During the working process of the punch press, the servo feed mechanism must start feeding after the machine tool slider is lifted. Before the slider falls, the feed mechanism must complete the positioning process. Therefore, it is required that the software part of the system must coordinate the movement between the slider of the machine tool and the feeding mechanism. The system uses the status query function of the MPC01 card to determine the position of the punch slider to determine whether to send a command to the servo motor for feed motion. In order to achieve the coordination between the slider and the feeding mechanism.
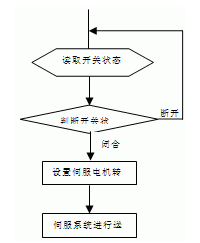
flow chart
The following is the motion control program for the feed system.
Private Sub Timer2_Timer()
Dim ch_status As Long
Dim a, b As Long
Ch_status = check_status(1)
/ Use the check_status function to read the status of the press home switch /
a = 4
b = a And ch_status
/ Judging if the origin switch is closed/
If b = 4 Then
/ If the origin switch is closed /
Set_conspeed 1, 100000
/ Call speed setting function set_conspeed to set the servo motor speed /
Con_pmove 1, Mdis* 835.8978246155
/ Call point movement function con_pmove to set the servo motor running direction and distance /
End If
End Sub
3. Conclusion After adopting the motion control card and servo feed system, this system effectively solved the high-precision positioning requirements and high-speed start requirements of the CNC punch press feed system, and developed a well-functioning user program in a very short time. , to meet the needs of the press application.
Red Dot Sight Height,Red Dot Sight Example,Red Dot Sight Lens,Red Dot Sight Takealot
Nantong Dinggo Optical Instrument Co.,Ltd , https://www.riflescopeofficial.com