The sensor (English name: transducer/sensor) is a detection device that can sense the measured information and can transform the sensed information into electrical signals or other desired forms of information output to meet the information. The requirements for transmission, processing, storage, display, recording and control.
The characteristics of the sensor include: miniaturization, digitization, intelligence, multifunction, systematization, and networking. It is the first link to achieve automatic detection and automatic control. The presence and development of sensors allows objects to have senses such as touch, taste, and smell, allowing objects to become alive. According to its basic perceptual functions, it can be divided into ten categories: thermal sensors, photosensitive sensors, gas sensors, force sensors, magnetic sensors, humidity sensors, acoustic sensors, radiation sensitive sensors, color sensors, and flavor sensors. .
Chinese name
sensor
Foreign name
Transducer/sensor
Features
Miniaturization, digitization, intelligence, etc.
First step
Realize automatic detection and automatic control
Nature
Detection device
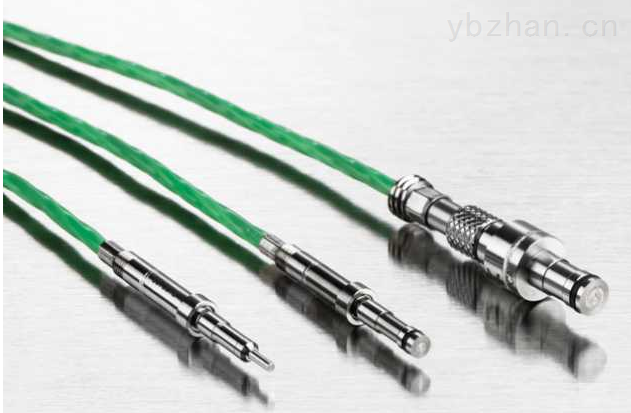
The national standard GB7665-87 defines the sensor as follows: “A device or device that can sense a specified part to be measured and convert it into a usable signal according to a certain law (a mathematical function rule), usually consisting of a sensitive element and a conversion elementâ€.
The China Internet of Things school-enterprise alliance believes that the presence and development of sensors will allow objects to have senses such as touch, taste, and smell, allowing objects to gradually become alive. â€
"Sensors" are defined in the New Wexar dictionary as: "Receive power from one system, usually sending power to devices in the second system in another form."
2 main roleIn order to obtain information from the outside world, people must rely on sensory organs.
And relying solely on people’s own sensory organs, their function in the study of natural phenomena and laws and production activities is far from enough. To meet this situation, sensors are needed. Therefore, it can be said that the sensor is an extension of human features, also known as electrical features.
With the arrival of the new technology revolution, the world has begun to enter the information age. In the process of using information, the first thing to solve is to obtain accurate and reliable information, and sensors are the main means and means for acquiring information in the natural and production fields.
In modern industrial production, especially in the automated production process, various sensors are used to monitor and control the various parameters in the production process so that the equipment can be operated in a normal state or an optimal state, and the products can achieve the best quality. Therefore, it can be said that without numerous excellent sensors, modern production loses its foundation.
In the study of basic disciplines, sensors have a more prominent position. The development of modern science and technology has entered many new fields: for example, macroscopic observations of the vast universe of thousands of light years, microcosmic observations of particle worlds as small as fm, and longitudinal observation of the evolution of celestial bodies for hundreds of thousands of years Short response to s. In addition, there have also emerged various kinds of extreme technological researches that have an important role in deepening the understanding of materials, developing new energy, and new materials, such as ultra-high temperature, ultra-low temperature, ultra-high pressure, ultra-high vacuum, super magnetic field, and ultra-weak magnetic field. Obviously, to get a lot of information that human senses cannot directly obtain, there is no suitable sensor. Obstacles to many basic scientific researches are the difficulty in obtaining object information. The emergence of some new mechanisms and high-sensitivity detection sensors will often lead to breakthroughs in this field. The development of some sensors is often a pioneer in the development of some marginal disciplines.
Sensors have already penetrated into an extremely wide range of fields such as industrial production, space development, ocean exploration, environmental protection, resource investigation, medical diagnosis, biological engineering, and even cultural heritage protection. It is no exaggeration to say that from the vastness of space, to the vast oceans, to a variety of complex engineering systems, almost every modern project can not be separated from a variety of sensors.
This shows that the important role of sensor technology in economic development and social progress is very obvious. All countries in the world attach great importance to the development of this field. It is believed that in the near future, sensor technology will take a leap forward and reach a new level commensurate with its important position.
3 main featuresThe characteristics of the sensors include: miniaturization, digitization, intelligence, multi-functionalization, systematization, and networking. It not only promotes the transformation and replacement of traditional industries, but also creates new industries, thus becoming a new economic growth in the 21st century. point. Miniaturization is based on micro-electro-mechanical system (MEMS) technology. Silicone pressure sensors have been successfully applied to silicon devices.
4 main functionsThe function of the sensor is often compared with the human 5 sense organs:
Photosensors - Vision
Acoustic sensor - hearing
Gas Sensor - Olfactory
Chemical Sensors - Taste
Pressure sensitive, temperature sensitive,
Fluid Sensor - Touch
Classification of sensitive components:
Physics, based on physical effects such as force, heat, light, electricity, magnetism, and sound.
Chemicals, based on the principle of chemical reactions.
Biological class, based on molecular recognition functions such as enzymes, antibodies, and hormones.
Usually based on its basic sense of function can be divided into thermal elements, photosensitive elements, gas sensors, force sensors, magnetic sensors, humidity sensors, acoustic sensors, radiation sensitive devices, color sensors and taste sensitive components, etc. Classes (and others have classified sensitive elements into 46 categories).
5 common types of resistanceA resistive sensor is a device that converts physical quantities such as displacement, deformation, force, acceleration, humidity, and temperature into resistance values. Mainly resistance strain type, piezoresistive type, thermal resistance, heat sensitive, gas sensitive, moisture sensitive and other resistive sensors.
Frequency conversion powerThe frequency conversion power sensor conducts ac sampling on the input voltage and current signals, and then connects the sampling value with a digital input secondary instrument through a transmission system such as a cable or an optical fiber. The digital input secondary instrument calculates the voltage and current sampling values. Can obtain voltage RMS, current rms, fundamental voltage, fundamental current, harmonic voltage, harmonic current, active power, fundamental power, harmonic power and other parameters.
WeighingThe load cell is a force → electrical conversion device that can convert gravity into an electrical signal and is a key component of the electronic scale.
There are many types of sensors that can achieve force-to-electrical conversion. The common ones are resistance strain type, electromagnetic force type, and capacitance type. Electromagnetic force type is mainly used in electronic balances, and capacitive type is used in some electronic hanging scales. The vast majority of weighing instruments use resistance strain type load cells. The resistance strain type load cell has a simple structure, high accuracy, wide application range, and can be used in a relatively poor environment. Therefore, the resistance strain load cell has been widely used in instruments.
Resistance strain typeThe strain gage in the sensor has a strain effect on the metal, that is, it generates a mechanical deformation under the action of an external force, thereby causing a corresponding change in the resistance value. Resistance strain gauges mainly include two kinds of metals and semiconductors. Metal strain gauges are classified into metal wire type, foil type, and film type. Semiconductor strain gauges have the advantages of high sensitivity (usually tens of times that of wire and foil type) and small lateral effects.
PiezoresistiveA piezoresistive sensor is a device made by diffusion resistance of a semiconductor material substrate based on the piezoresistive effect of a semiconductor material. The substrate can be directly used as a measuring sensor element, and the diffusion resistor is formed in the form of a bridge in the substrate. When the substrate is deformed by an external force, the resistance will change and the bridge will produce a corresponding unbalanced output.
The substrate (or diaphragm) used as a piezoresistive sensor is mainly composed of silicon wafers and tantalum wafers. Silicon piezoresistive sensors made of silicon as sensitive materials are receiving more and more attention, especially in measuring pressure. Solid-state piezoresistive sensors with speed and speed are most commonly used.
Thermal resistanceThermal resistance temperature measurement is based on the characteristic that the resistance value of a metal conductor increases as the temperature increases.
Most of the thermal resistance is made of pure metal materials. Currently, platinum and copper are the most widely used materials. In addition, nickel, manganese, and tantalum have been used to manufacture thermal resistors.
Thermistor sensors measure the temperature and temperature-related parameters by taking advantage of the fact that resistance changes with temperature. This sensor is suitable for applications where the accuracy of temperature detection is relatively high. The wide range of thermal resistance materials are platinum, copper, nickel, etc. They have the characteristics of large temperature coefficient of resistance, good linearity, stable performance, wide operating temperature range, and easy processing. Used to measure temperatures in the range of -200°C to +500°C.
Thermal resistance sensor classification:
1, NTC thermal resistance sensor:
This type of sensor is a negative temperature coefficient sensor, that is, the sensor resistance decreases with increasing temperature.
2, PTC thermal resistance sensor:
This type of sensor is a positive temperature coefficient sensor, that is, the resistance of the sensor increases as the temperature increases.
laserSensors that measure using laser technology.
It consists of a laser, a laser detector and a measuring circuit. The laser sensor is a new type of measuring instrument. Its advantages are that it can realize non-contact long-distance measurement, high speed, high precision, large range, and strong resistance to light and electricity. When the laser sensor is working, the laser emitting diode is aimed at the target emitting laser pulse. The target reflected laser light scattered in all directions. Part of the scattered light is returned to the sensor receiver, which is received by the optical system and imaged onto an avalanche photodiode. An avalanche photodiode is an optical sensor with an internal amplification function, so it can detect extremely weak light signals and convert them into corresponding electrical signals.
The use of lasers with high directionality, high monochromaticity and high brightness enables contactless distance measurements. Laser sensors are commonly used for measuring physical quantities such as length (ZLS-Px), distance (LDM4x), vibration (ZLDS10X), velocity (LDM30x), azimuth, etc., and can also be used for flaw detection and air pollutant monitoring.
HallHall sensor is a kind of magnetic field sensor based on Hall effect, which is widely used in industrial automation technology, detection technology and information processing. Hall effect is the basic method for studying the properties of semiconductor materials. The Hall coefficient measured by the Hall effect experiment can determine important parameters such as conductivity type, carrier concentration, and carrier mobility of the semiconductor material.
Hall sensors are classified into linear Hall sensors and switch Hall sensors.
1. The linear Hall sensor consists of a Hall element, a linear amplifier, and an emitter follower, which outputs an analog quantity.
2. The switch Hall sensor consists of a voltage regulator, a Hall element, a differential amplifier, a Schmitt trigger, and an output stage. It outputs a digital quantity.
The Hall voltage changes with the change of the magnetic field strength. The stronger the magnetic field, the higher the voltage, the weaker the magnetic field and the lower the voltage. The Hall voltage is very small, typically only a few millivolts, but it can be amplified by an amplifier in an integrated circuit to produce a strong signal. If Hall ICs are used for sensing, it is necessary to use mechanical methods to change the magnetic field strength. The method shown in the following figure uses a rotating impeller as a switch to control the magnetic flux. When the impeller blade is in the air gap between the magnet and the Hall IC, the magnetic field deviates from the integrated chip and the Hall voltage disappears. In this way, the change of the output voltage of the Hall IC can indicate a certain position of the impeller drive shaft. Using this working principle, the Hall IC chip can be used to act on the ignition timing sensor. Hall effect sensors are passive sensors that require an external power source to operate. This feature makes it possible to detect low operating speeds.
temperature1. Room-temperature tube temperature sensor: The room temperature sensor is used to measure the indoor and outdoor ambient temperature, and the tube temperature sensor is used to measure the wall temperature of the evaporator and the condenser. The shape of the room temperature sensor and the tube temperature sensor are different, but the temperature characteristics are basically the same. According to the temperature characteristics, there are two types of room temperature tube temperature sensors used by Midea: 1. The constant B value is 4100K±3%, and the reference resistance is 25°C corresponding resistance 10KΩ±3%. The tolerances for the resistors at 0°C and 55°C are approximately ±7%. For resistors below 0°C and 55°C, the tolerance of the resistors will be different. The higher the temperature, the smaller the resistance; the lower the temperature, the greater the resistance. The further away from 25°C, the larger the corresponding resistance tolerance range.
2. Exhaust temperature sensor: The exhaust temperature sensor is used to measure the exhaust temperature at the top of the compressor. The constant B value is 3950K±3%, and the reference resistance is 90°C corresponding resistance 5KΩ±3%.
3. Module temperature sensor: The module temperature sensor is used to measure the temperature of the inverter module (IGBT or IPM). The type of the temperature sensor head used is 602F-3500F and the reference resistor is 25°C corresponding resistor 6KΩ±1%. The corresponding resistance of several typical temperatures are: -10°C→(25.897─28.623)KΩ; 0°C→(16.3248─17.7164)KΩ; 50°C→(2.3262─2.5153)KΩ; 90°C→(0.6671─0.7565) KΩ.
There are many kinds of temperature sensors, often used thermal resistance: PT100, PT1000, Cu50, Cu100; thermocouple: B, E, J, K, S and so on. The temperature sensors are not only diverse in variety, but also in a variety of combinations, and suitable products should be selected according to different locations.
Principle of temperature measurement: According to the principle that the resistance of the resistor and the potential of the thermocouple change regularly with temperature, we can obtain the measured temperature value.
Wireless temperatureThe wireless temperature sensor converts the temperature parameter of the control object into an electrical signal and sends a wireless signal to the receiving terminal to perform detection, adjustment, and control of the system. It can be directly installed in the junction boxes of general industrial thermal resistance and thermocouples, and it is integrated with the on-site sensing elements. It is usually used together with wireless relay, receiving terminal, communication serial port, electronic computer, etc. This not only saves compensation wires and cables, but also reduces signal transmission distortion and interference, and thus obtains high-precision measurement results.
Wireless temperature sensors are widely used in chemical, metallurgical, petroleum, electric power, water treatment, pharmaceutical, food and other automation industries. For example: temperature acquisition on high-voltage cables; temperature acquisition in harsh environments such as underwater; temperature acquisition on moving objects; transmission of sensor data in spaces that are difficult to pass through; data acquisition schemes that are purely used to reduce wiring costs; no AC power supply Workplace data measurement; Portable non-stationary data measurement.
intelligentThe function of the smart sensor is proposed by simulating human sensory and brain coordination actions, combined with long-term research and practical experience in test technology. Is a relatively independent smart unit, its emergence of the original hardware performance requirements have been reduced, while the help of software can greatly improve the performance of the sensor.
1, information storage and transmission - with the rapid development of smart distributed control system (SmartDistributedSystem), the smart unit requires a communication function, the use of communication networks for digital two-way communication, which is one of the key indicators of smart sensors. Smart sensors implement various functions by testing data transmission or receiving instructions. Such as gain setting, compensation parameter setting, internal inspection parameter setting, test data output, etc.
2. Self-compensation and calculation functions—Engineers and technicians engaged in sensor development for many years have been doing a lot of compensation work for sensor temperature drift and output nonlinearity, but they have not solved the problem fundamentally. The self-compensation and calculation functions of smart sensors open up a new path for sensor temperature drift and nonlinear compensation. In this way, to relax the sensor processing precision, as long as the repeatability of the sensor can be ensured, the signal of the test signal is calculated by the microprocessor through software, and the drift and the nonlinearity are compensated by the multiple fitting and the difference calculation method, so that the Get more accurate measurement pressure sensors.
3, self-test, self-school, self-diagnosis function - ordinary sensors need regular inspection and calibration, to ensure that it is sufficient accuracy in normal use, these tasks generally require the sensor to be disassembled from the use of the site to the laboratory or inspection department get on. If the online measurement sensor is abnormal, it cannot be diagnosed in time. The situation with smart sensors is greatly improved. First, the self-diagnosis function performs self-test when the power is turned on, and diagnostic tests are performed to determine whether the components are faulty. Secondly, it can be calibrated on-line according to the time of use. The microprocessor uses the metering characteristic data stored in the EPROM for comparison and proofreading.
4, compound sensitive function - observe the surrounding natural phenomena, common signals sound, light, electricity, heat, force, chemistry and so on. Sensing element measurements generally take two forms: direct and indirect measurements. The smart sensor has a complex function that can simultaneously measure a variety of physical and chemical quantities, giving information that can fully reflect the law of motion of the material.
PhotosensitivePhotosensitive sensor is one of the most common sensors. It has a wide range of types, including photocells, photomultipliers, photoresistors, phototransistors, solar cells, infrared sensors, ultraviolet sensors, fiber optic sensors, color sensors, and CCDs. CMOS image sensors, etc. Its sensitive wavelength is near the visible light wavelength, including infrared wavelength and ultraviolet wavelength. The optical sensor is not limited to the detection of light. It can also be used as a detection element to form other sensors and detect many non-electrical quantities. It is only necessary to convert these non-electrical quantities into changes in the optical signal. Optical sensor is one of the most widely used and most widely used sensors at present. It plays a very important role in automatic control and non-electricity measurement. The simplest photosensitive sensor is a photoresistor, which generates current when the photons strike the junction.
biologicalBiosensor concept
Biosensors are an interdisciplinary subject that combines biologically active materials (enzymes, proteins, DNA, antibodies, antigens, biofilms, etc.) and physico-chemical transducers. It is an advanced detection method that is essential for the development of biotechnology. And monitoring methods are also fast and micro-analytical methods for the molecular level of matter. Various types of biosensors have the following common structures: one or more related bioactive materials (biofilms) and physical or chemical transducers (sensors) capable of converting signals expressed by bioactivity into electrical signals. Together, the reprocessing of biological signals using modern microelectronics and automated instrumentation technologies constitutes a variety of biosensor analysis devices, instruments, and systems that can be used.
The principle of biosensors
The substance to be tested enters the biologically active material through diffusion and undergoes a biological reaction through molecular recognition. The resulting information is then converted into a quantifiable and processable electrical signal by a corresponding physical or chemical transducer, and then amplified by the secondary instrument. And output, you can know the analyte concentration.
Classification of biosensors
According to the classification of living substances used in its receptors, it can be divided into: microbial sensors, immunosensors, tissue sensors, cell sensors, enzyme sensors, DNA sensors, and the like.
Classification according to the principle of sensor device detection, can be divided into: thermal biosensor, FET biosensor, piezoelectric biosensor, optical biosensor, acoustic channel biosensor, enzyme electrode biosensor, mediator biosensor and so on.
According to the type of interaction of biologically sensitive substances, they can be divided into two types: affinity type and metabolic type.
Visionworking principle:
The visual sensor refers to the ability to capture thousands of pixels from a whole image, and the resolution of the image is usually measured in terms of the number of pixels.
Vision sensors have thousands of pixels that capture light from an entire image. The clarity and sophistication of an image is usually measured in terms of resolution, expressed in number of pixels.
After the image is captured, the vision sensor compares it with a reference image stored in memory for analysis. For example, if the vision sensor is set to identify a machine part with eight bolts correctly inserted, the sensor knows that only seven bolts should be rejected, or that the bolts are misaligned. In addition, the visual sensor can make a decision regardless of the position of the machine component in the field of view, whether or not the component rotates within 360 degrees.
Application area:
The low cost and ease of use of vision sensors has attracted machine designers and process engineers to integrate them into a variety of applications that have relied on labor, multiple photo sensors, or have not been tested at all. Industrial applications of vision sensors include inspection, metrology, measurement, orientation, helium detection, and delivery. The following are just a few examples of applications:
At the automobile assembly plant, check whether the plastic beads applied to the door frame by the robot are continuous and have the correct width.
At the bottling plant, verify that the cap is properly sealed, that the fill level is correct, and that no foreign objects have fallen into the bottle prior to capping;
In the packaging line, ensure that the correct packaging label is affixed to the correct location;
In the pharmaceutical packaging line, whether there are broken or missing tablets in the blister pack of aspirin tablets;
In the metal stamping company, stamped parts are inspected at a speed of more than 150 sheets per minute, which is 13 times faster than manual inspection.
DisplacementDisplacement sensor, also known as a linear sensor, converts displacement into a sensor of electrical quantity. Displacement sensor is a kind of linear device that belongs to metal induction. The function of sensor is to convert various measured physical quantities into electricity. It is divided into inductive displacement sensor, capacitive displacement sensor, photoelectric displacement sensor, ultrasonic displacement sensor, Hall. Displacement sensor.
In this conversion process there are many physical quantities (such as pressure, flow, acceleration, etc.) often need to be transformed into displacement, and then convert the displacement into electricity. Therefore, the displacement sensor is an important basic sensor. In the production process, the displacement measurement is generally divided into measuring the physical size and the mechanical displacement. Mechanical displacements include line and angular displacements. According to the different forms of measured variables, displacement sensors can be divided into analog and digital two. Simulation can be divided into physical (such as self-generating) and structural two. Commonly used displacement sensors are mostly analog ones, including potentiometer-type displacement sensors, inductive displacement sensors, self-segment anglers, capacitive displacement sensors, eddy current displacement sensors, and Hall-type displacement sensors. An important advantage of a digital displacement sensor is that it facilitates the direct feeding of signals into computer systems. This sensor has developed rapidly and has become more widely used.
pressurePressure sensor cited is the most commonly used sensor in industrial practice. It is widely used in various industrial automation environments, involving water conservancy and hydropower, railway transportation, intelligent buildings, production automation, aerospace, military, petrochemical, oil wells, electricity, ships, Machine tools, pipelines and many other industries.
Ultrasonic distance measurementThe ultrasonic distance measuring sensor adopts the principle of ultrasonic echo distance measurement. It uses precise time difference measurement technology to detect the distance between the sensor and the target. It adopts a small angle, small blind ultrasonic sensor with accurate measurement, no contact, waterproof and anti-corrosion. The advantages of low cost, such as liquid level, level detection, unique liquid level, material level detection method, can ensure that there is foam or large shaking on the liquid surface, and there is a stable output when the echo is not easily detected. Application industry: level, level, material level detection, industrial process control, etc.
24GHz radar24GHz radar sensor uses high-frequency microwaves to measure the speed, distance, and movement of objects
RFbeam 24GHz Radar Sensor
The direction and azimuth angle information adopts the planar microstrip antenna design, featuring small size, light weight, high sensitivity, and strong stability. It is widely used in intelligent transportation, industrial control, security, sports, and smart home industries. On November 19, 2012, the Ministry of Industry and Information Technology formally released the "Ministry of Industry and Information Technology Released a Notice Concerning the Release of Vehicle-mounted Radar Equipment Usage Frequencies at Short Range from the 24GHz Frequency Band" (Ministry of Industry and Information Technology No. No. [2012] No. 548), which explicitly stated that the 24 GHz band is short-range. Car radar equipment as a vehicle radar equipment specification.
Integrated temperatureIntegrated temperature sensors generally consist of a temperature probe (thermocouple or RTD sensor) and two-wire solid state electronics. The solid-state module is used to mount the temperature probe directly in the junction box to form an integrated sensor. Integrated temperature sensors are generally classified into two types: thermal resistance and thermocouple type.
Thermal resistance temperature sensor is composed of reference unit, R/V conversion unit, linear circuit, reverse connection protection, current limit protection, V/I conversion unit and so on. After the temperature-resistor resistance signal is converted and amplified, the linear circuit compensates the nonlinear relationship between the temperature and the resistance. After the V/I conversion circuit, a constant current signal of 4-20 mA which is in a linear relationship with the measured temperature is output.
Thermocouple temperature sensor is generally composed of a reference source, cold junction compensation, amplification unit, linearization, V / I conversion, burnout processing, reverse connection protection, current limiting protection and other circuit units. It is the thermal potential generated by the thermocouple through the cold-end compensation after amplification, and then cap the linear circuit to eliminate the thermal potential and temperature of the nonlinear error, and finally amplified into 4 ~ 20mA current output signal. In order to prevent accidents caused by temperature control failure due to galvanic disconnection in thermocouple measurement, a power failure protection circuit is also provided in the sensor. When the thermocouple breaks or fails to connect, the sensor will output the maximum value (28mA) to make the meter cut off the power. The integrated temperature sensor has the advantages of simple structure, saving lead wire, large output signal, strong anti-interference ability, good linearity, simple display instrument, solid module moisture resistance, reverse connection protection and current limit protection, and reliable work. The output of the integrated temperature sensor is a unified 4-20mA signal; it can be used with a microcomputer system or other conventional instruments. Can also be made of explosion-proof or fire-proof measuring instruments.
Liquid level1ã€Floating ball level sensor
The float level sensor is composed of a magnetic float, a measurement catheter, a signal unit, an electronic unit, a junction box, and a mounting member.
Generally, the specific gravity of the magnetic float is less than 0.5, and it can float on the liquid surface and move up and down along the measuring tube. The catheter is equipped with a measuring element, which can convert the measured liquid level signal into a resistance signal proportional to the change of liquid level under the action of external magnetic flux, and converts the electronic unit into 4-20 mA or other standard signal output. The sensor is a module circuit, which has the advantages of acid resistance, moisture resistance, shockproof, anti-corrosion, etc. The circuit contains a constant current feedback circuit and an internal protection circuit, so that the maximum output current does not exceed 28mA, so it can reliably protect the power supply and make the secondary instrument Not damaged.
2, floating type liquid level sensor
The buoyancy level sensor is to change the magnetic float to buoy, which is designed according to the Archimedes buoyancy principle. Float type liquid level sensors use tiny metal film strain sensing technology to measure liquid level, boundary level, or density. It can use the on-site buttons to perform routine setup operations while working.
3, static pressure or liquid level sensor
The sensor works with the principle of hydrostatic pressure measurement. It generally selects the silicon pressure pressure sensor to convert the measured pressure into an electric signal, and then compensates by the amplifying circuit and the compensating circuit, and finally outputs the current by 4-20 mA or 0-10 mA.
Vacuum degreeVacuum level sensor, manufactured using advanced silicon micromachining technology, is an absolute pressure transmitter made of a silicon pressure resistive element as the core element of the sensor due to the use of silicon-silicon direct bonding or silicon-pyrox glass static electricity The vacuum reference pressure chamber formed by bonding, and a series of non-stressed encapsulation technologies and precision temperature compensation technologies have excellent advantages of excellent stability and high precision, and are suitable for measurement and control of absolute pressure in various situations.
Features and uses
Low-capacity chip vacuum vacuum package, the product has a high overload capacity. The chip is vacuum-filled with silicone oil, and the stainless steel film transfers pressure with excellent media compatibility. It is suitable for vacuum pressure measurement of most gas-liquid media that are not corroded by 316L stainless steel. The degree of vacuum is used to infect low vacuum measurement and control in various industrial environments.
Capacitive levelCapacitive level sensor is suitable for industrial enterprises to measure and control the production process during the production process. It is mainly used as a continuous measurement and indication for remote distances of liquid level or powdered solid material level in conductive and non-conductive media.
The capacitive liquid level sensor is composed of a capacitive sensor and an electronic module circuit. It uses a two-wire constant current output of 4 to 20 mA as a basic type. After conversion, it can be output in a three-wire or four-wire mode, and the output signal is formed as 1 to 5 V. 0 ~ 5V, 0 ~ 10mA and other standard signals. The capacitive sensor consists of an insulated electrode and a cylindrical metal vessel equipped with a measuring medium. When the material level rises, the dielectric constant of the non-conductive material is significantly smaller than the dielectric constant of air, so the capacitance changes with the height of the material. The module circuit of the sensor is composed of reference source, pulse width modulation, conversion, constant current amplification, feedback and current limiting units. The advantage of using the pulse width modulation principle to measure is that it has a low frequency, interference with ambient radio frequency, good stability, good linearity, and no significant temperature drift.
Electrode acidityThe 锑 electrode acidity sensor is an industrial on-line analysis instrument that integrates PH detection, automatic cleaning, and electrical signal conversion. It is a PH value measurement system consisting of a helium electrode and a reference electrode. In the measured acidic solution, a germanium trioxide oxide layer is formed on the surface of the germanium electrode, so that a potential difference is formed between the germanium surface and the germanium oxide. The magnitude of this potential difference depends on the concentration of trioxotide, which corresponds to the appropriate level of hydrogen ions in the acidic solution being tested. If the appropriateness of yttrium, yttria and aqueous solution is taken as 1, the electrode potential can be calculated using the Nernst formula.
The solid module circuit in the pH sensor consists of two major components. For the sake of safety in the field, the power supply uses AC 24V to power the secondary instrument. In addition to supplying power to the cleaning motor, this power supply should also be converted into a corresponding DC voltage by the current conversion unit for use by the transmission circuit. The second part is the measurement sensor circuit, which sends the reference signal from the sensor and PH acidity signal to the slope adjustment and positioning adjustment circuit after amplification, so that the signal internal resistance can be reduced and can be adjusted. The amplified PH signal and the temperature compensated signal are superposed and then converted into the conversion circuit. Finally, the 4-20 mA constant current signal corresponding to the PH value is output to the secondary meter to complete the display and control the PH value.
Acid, alkali, saltThe acid, alkali, and salt concentration sensors determine the concentration by measuring the conductance of the solution. It can continuously monitor the concentration of acid, alkali and salt in aqueous solution in the industrial process. This sensor is mainly used in boiler water treatment, chemical solution preparation and environmental protection and other industrial production processes.
The working principle of the acid, alkali, and salt concentration sensors is that within a certain range, the concentration of the acid-base solution is proportional to the size of its electrical conductivity. Therefore, as long as the measurement of the conductivity of the solution changes, the concentration of acid and alkali can be known. When the measured solution flows into a dedicated conductivity cell, if the electrode polarization and distributed capacitance are ignored, it can be equivalent to a pure resistance. When there is a constant voltage alternating current flowing, the output current is linear with the conductivity, and the conductivity is proportional to the concentration of acid and alkali in the solution. Therefore, as long as the solution current is measured, the concentration of acid, alkali and salt can be calculated.
The acid, alkali, and salt concentration sensors mainly consist of a conductivity cell, an electronic module, a display head, and a housing. The electronic module circuit is composed of excitation power supply, conductivity cell, conductance amplifier, phase sensitive rectifier, demodulator, temperature compensation, overload protection and current conversion.
ConductanceIt is a process meter (integrated sensor) that measures the ion concentration indirectly by measuring the conductance value of a solution, and can continuously detect the conductivity of an aqueous solution in an industrial process on-line.
Because the electrolyte solution is the same good electrical conductor as the metal conductor, there must be an electrical resistance when the current flows through the electrolyte solution, and it is in accordance with Ohm's law. However, the resistance temperature characteristics of liquids are contrary to those of metal conductors and have negative temperature characteristics. In order to distinguish from the metal conductor, the conductivity of the electrolyte solution is represented by conductance (reciprocal of resistance) or conductivity (reciprocal of resistivity). When two electrodes that are insulated from each other form a conductivity cell, a current loop is formed if the solution to be measured is placed in between, and a constant voltage alternating current is passed through. If the voltage size and the electrode size are fixed, the loop current and the conductivity have a certain function. In this way, measuring the current flowing in the solution to be measured, the conductivity of the solution to be measured can be measured. The conductivity sensor has the same structure and circuit as the acid, alkali, and salt concentration sensors.
6 major classification by purposePressure sensitive and force sensitive sensors, position sensors, level sensors, energy sensors, speed sensors, acceleration sensors, ray radiation sensors, thermal sensors.
By principleVibration sensor, humidity sensor, magnetic sensor, gas sensor, vacuum sensor, biosensor, etc.
Press output signalAnalog sensors: Convert the non-electrical quantities that are measured into analog electrical signals.
Digital Sensors: Convert the measured non-electrical quantities into digital output signals (including direct and indirect conversions).
膺 digital sensor: The amount of signal to be measured is converted to the output of a frequency signal or short-cycle signal (including direct or indirect conversion).
Switch sensor: When a measured signal reaches a certain threshold, the sensor outputs a set low or high signal accordingly.
According to its manufacturing processIntegrated sensors are manufactured using standard process technologies for producing silicon-based semiconductor integrated circuits.
Parts of the circuits that are used to initially process the measured signal are also typically integrated on the same chip.
The thin film sensor is formed by a thin film of a corresponding sensitive material deposited on a dielectric substrate (substrate). When using a hybrid process, some circuits can also be fabricated on this substrate.
The thick film sensor is made by coating a ceramic substrate with a slurry of a corresponding material. The substrate is usually made of Al2O3 and then heat-treated to form a thick film.
Ceramic sensors are produced using a standard ceramic process or some variant process (sol, gel, etc.).
After an appropriate preliminary operation is completed, the formed element is sintered at a high temperature. There are many common characteristics between the two processes of thick film and ceramic sensor. In some aspects, it can be considered that the thick film process is a variation of the ceramic process.
Each process technology has its own advantages and disadvantages. Due to the low capital investment required for research, development and production, as well as the high stability of sensor parameters, it is reasonable to use ceramic and thick-film sensors.
By measurementPhysical sensors are made using properties where the physical properties of the material being measured change significantly.
Chemical sensors are made using sensitive elements that convert the chemical composition and concentration into electrical quantities.
Biosensors are sensors that use various biological or biological properties to detect and identify chemical constituents in living organisms.
According to its compositionBasic sensor: It is the most basic single transducer.
Combination sensor: A sensor that consists of a combination of different individual transducers.
Application sensor: A sensor that is a combination of a basic sensor or a combination sensor and other mechanisms.
According to the form of action按作用形å¼å¯åˆ†ä¸ºä¸»åŠ¨åž‹å’Œè¢«åŠ¨åž‹ä¼ æ„Ÿå™¨ã€‚
ä¸»åŠ¨åž‹ä¼ æ„Ÿå™¨åˆæœ‰ä½œç”¨åž‹å’Œå作用型,æ¤ç§ä¼ 感器对被测对象能å‘出一定探测信å·ï¼Œèƒ½æ£€æµ‹æŽ¢æµ‹ä¿¡å·åœ¨è¢«æµ‹å¯¹è±¡ä¸æ‰€äº§ç”Ÿçš„å˜åŒ–,或者由探测信å·åœ¨è¢«æµ‹å¯¹è±¡ä¸äº§ç”ŸæŸç§æ•ˆåº”而形æˆä¿¡å·ã€‚检测探测信å·å˜åŒ–æ–¹å¼çš„称为作用型,检测产生å“应而形æˆä¿¡å·æ–¹å¼çš„称为åä½œç”¨åž‹ã€‚é›·è¾¾ä¸Žæ— çº¿ç”µé¢‘çŽ‡èŒƒå›´æŽ¢æµ‹å™¨æ˜¯ä½œç”¨åž‹å®žä¾‹ï¼Œè€Œå…‰å£°æ•ˆåº”åˆ†æžè£…置与激光分æžå™¨æ˜¯å作用型实例。
è¢«åŠ¨åž‹ä¼ æ„Ÿå™¨åªæ˜¯æŽ¥æ”¶è¢«æµ‹å¯¹è±¡æœ¬èº«äº§ç”Ÿçš„ä¿¡å·ï¼Œå¦‚红外è¾å°„温度计ã€çº¢å¤–æ‘„åƒè£…ç½®ç‰ã€‚
7主è¦ç‰¹æ€§ä¼ æ„Ÿå™¨é™æ€ä¼ æ„Ÿå™¨çš„é™æ€ç‰¹æ€§æ˜¯æŒ‡å¯¹é™æ€çš„输入信å·ï¼Œä¼ 感器的输出é‡ä¸Žè¾“å…¥é‡ä¹‹é—´æ‰€å…·æœ‰ç›¸äº’å…³ç³»ã€‚å› ä¸ºè¿™æ—¶è¾“å…¥é‡å’Œè¾“出é‡éƒ½å’Œæ—¶é—´æ— 关,所以它们之间的关系,å³ä¼ æ„Ÿå™¨çš„é™æ€ç‰¹æ€§å¯ç”¨ä¸€ä¸ªä¸å«æ—¶é—´å˜é‡çš„代数方程,或以输入é‡ä½œæ¨ªåæ ‡ï¼ŒæŠŠä¸Žå…¶å¯¹åº”çš„è¾“å‡ºé‡ä½œçºµåæ ‡è€Œç”»å‡ºçš„ç‰¹æ€§æ›²çº¿æ¥æè¿°ã€‚è¡¨å¾ä¼ æ„Ÿå™¨é™æ€ç‰¹æ€§çš„主è¦å‚数有:线性度ã€çµæ•度ã€è¿Ÿæ»žã€é‡å¤æ€§ã€æ¼‚ç§»ç‰ã€‚
1ã€çº¿æ€§åº¦ï¼šæŒ‡ä¼ 感器输出é‡ä¸Žè¾“å…¥é‡ä¹‹é—´çš„实际关系曲线å离拟åˆç›´çº¿çš„程度。定义为在全é‡ç¨‹èŒƒå›´å†…实际特性曲线与拟åˆç›´çº¿ä¹‹é—´çš„æœ€å¤§å差值与满é‡ç¨‹è¾“出值之比。
2ã€çµæ•åº¦ï¼šçµæ•åº¦æ˜¯ä¼ æ„Ÿå™¨é™æ€ç‰¹æ€§çš„一个é‡è¦æŒ‡æ ‡ã€‚其定义为输出é‡çš„增é‡ä¸Žå¼•起该增é‡çš„相应输入é‡å¢žé‡ä¹‹æ¯”。用Sè¡¨ç¤ºçµæ•度。
3ã€è¿Ÿæ»žï¼šä¼ 感器在输入é‡ç”±å°åˆ°å¤§ï¼ˆæ£è¡Œç¨‹ï¼‰åŠè¾“å…¥é‡ç”±å¤§åˆ°å°ï¼ˆå行程)å˜åŒ–期间其输入输出特性曲线ä¸é‡åˆçš„现象æˆä¸ºè¿Ÿæ»žã€‚对于åŒä¸€å¤§å°çš„输入信å·ï¼Œä¼ 感器的æ£å行程输出信å·å¤§å°ä¸ç›¸ç‰ï¼Œè¿™ä¸ªå·®å€¼ç§°ä¸ºè¿Ÿæ»žå·®å€¼ã€‚
4ã€é‡å¤æ€§ï¼šé‡å¤æ€§æ˜¯æŒ‡ä¼ æ„Ÿå™¨åœ¨è¾“å…¥é‡æŒ‰åŒä¸€æ–¹å‘作全é‡ç¨‹è¿žç»å¤šæ¬¡å˜åŒ–时,所得特性曲线ä¸ä¸€è‡´çš„程度。
5ã€æ¼‚ç§»ï¼šä¼ æ„Ÿå™¨çš„æ¼‚ç§»æ˜¯æŒ‡åœ¨è¾“å…¥é‡ä¸å˜çš„æƒ…å†µä¸‹ï¼Œä¼ æ„Ÿå™¨è¾“å‡ºé‡éšç€æ—¶é—´å˜åŒ–,æ¤çŽ°è±¡ç§°ä¸ºæ¼‚ç§»ã€‚äº§ç”Ÿæ¼‚ç§»çš„åŽŸå› æœ‰ä¸¤ä¸ªæ–¹é¢ï¼šä¸€æ˜¯ä¼ æ„Ÿå™¨è‡ªèº«ç»“æž„å‚æ•°ï¼›äºŒæ˜¯å‘¨å›´çŽ¯å¢ƒï¼ˆå¦‚æ¸©åº¦ã€æ¹¿åº¦ç‰ï¼‰ã€‚
6ã€åˆ†è¾¨åŠ›ï¼šå½“ä¼ æ„Ÿå™¨çš„è¾“å…¥ä»Žéžé›¶å€¼ç¼“æ…¢å¢žåŠ æ—¶ï¼Œåœ¨è¶…è¿‡æŸä¸€å¢žé‡åŽè¾“出å‘生å¯è§‚测的å˜åŒ–,这个输入增é‡ç§°ä¼ æ„Ÿå™¨çš„åˆ†è¾¨åŠ›ï¼Œå³æœ€å°è¾“入增é‡ã€‚
7ã€é˜ˆå€¼ï¼šå½“ä¼ æ„Ÿå™¨çš„è¾“å…¥ä»Žé›¶å€¼å¼€å§‹ç¼“æ…¢å¢žåŠ æ—¶ï¼Œåœ¨è¾¾åˆ°æŸä¸€å€¼åŽè¾“出å‘生å¯è§‚测的å˜åŒ–ï¼Œè¿™ä¸ªè¾“å…¥å€¼ç§°ä¼ æ„Ÿå™¨çš„é˜ˆå€¼ç”µåŽ‹ã€‚
ä¼ æ„Ÿå™¨åŠ¨æ€æ‰€è°“动æ€ç‰¹æ€§ï¼Œæ˜¯æŒ‡ä¼ 感器在输入å˜åŒ–时,它的输出的特性。在实际工作ä¸ï¼Œä¼ 感器的动æ€ç‰¹æ€§å¸¸ç”¨å®ƒå¯¹æŸäº›æ ‡å‡†è¾“入信å·çš„å“应æ¥è¡¨ç¤ºã€‚è¿™æ˜¯å› ä¸ºä¼ æ„Ÿå™¨å¯¹æ ‡å‡†è¾“å…¥ä¿¡å·çš„å“åº”å®¹æ˜“ç”¨å®žéªŒæ–¹æ³•æ±‚å¾—ï¼Œå¹¶ä¸”å®ƒå¯¹æ ‡å‡†è¾“å…¥ä¿¡å·çš„å“应与它对任æ„输入信å·çš„å“应之间å˜åœ¨ä¸€å®šçš„关系,往往知é“了å‰è€…就能推定åŽè€…ã€‚æœ€å¸¸ç”¨çš„æ ‡å‡†è¾“å…¥ä¿¡å·æœ‰é˜¶è·ƒä¿¡å·å’Œæ£å¼¦ä¿¡å·ä¸¤ç§ï¼Œæ‰€ä»¥ä¼ 感器的动æ€ç‰¹æ€§ä¹Ÿå¸¸ç”¨é˜¶è·ƒå“应和频率å“应æ¥è¡¨ç¤ºã€‚
çº¿æ€§åº¦é€šå¸¸æƒ…å†µä¸‹ï¼Œä¼ æ„Ÿå™¨çš„å®žé™…é™æ€ç‰¹æ€§è¾“å‡ºæ˜¯æ¡æ›²çº¿è€Œéžç›´çº¿ã€‚在实际工作ä¸ï¼Œä¸ºä½¿ä»ªè¡¨å…·æœ‰å‡åŒ€åˆ»åº¦çš„è¯»æ•°ï¼Œå¸¸ç”¨ä¸€æ¡æ‹Ÿåˆç›´çº¿è¿‘似地代表实际的特性曲线ã€çº¿æ€§åº¦ï¼ˆéžçº¿æ€§è¯¯å·®ï¼‰å°±æ˜¯è¿™ä¸ªè¿‘ä¼¼ç¨‹åº¦çš„ä¸€ä¸ªæ€§èƒ½æŒ‡æ ‡ã€‚
拟åˆç›´çº¿çš„选喿œ‰å¤šç§æ–¹æ³•。如将零输入和满é‡ç¨‹è¾“出点相连的ç†è®ºç›´çº¿ä½œä¸ºæ‹Ÿåˆç›´çº¿ï¼›æˆ–将与特性曲线上å„点å差的平方和为最å°çš„ç†è®ºç›´çº¿ä½œä¸ºæ‹Ÿåˆç›´çº¿ï¼Œæ¤æ‹Ÿåˆç›´çº¿ç§°ä¸ºæœ€å°äºŒä¹˜æ³•拟åˆç›´çº¿ã€‚
Sensitivityçµæ•åº¦æ˜¯æŒ‡ä¼ æ„Ÿå™¨åœ¨ç¨³æ€å·¥ä½œæƒ…况下输出é‡å˜åŒ–â–³y对输入é‡å˜åŒ–â–³x的比值。
å®ƒæ˜¯è¾“å‡ºä¸€è¾“å…¥ç‰¹æ€§æ›²çº¿çš„æ–œçŽ‡ã€‚å¦‚æžœä¼ æ„Ÿå™¨çš„è¾“å‡ºå’Œè¾“å…¥ä¹‹é—´æ˜¾çº¿æ€§å…³ç³»ï¼Œåˆ™çµæ•度S是一个常数。å¦åˆ™ï¼Œå®ƒå°†éšè¾“å…¥é‡çš„å˜åŒ–而å˜åŒ–。
çµæ•度的é‡çº²æ˜¯è¾“出ã€è¾“å…¥é‡çš„é‡çº²ä¹‹æ¯”。例如,æŸä½ç§»ä¼ 感器,在ä½ç§»å˜åŒ–1mm时,输出电压å˜åŒ–为200mVï¼Œåˆ™å…¶çµæ•度应表示为200mV/mm。
å½“ä¼ æ„Ÿå™¨çš„è¾“å‡ºã€è¾“å…¥é‡çš„é‡çº²ç›¸åŒæ—¶ï¼Œçµæ•度å¯ç†è§£ä¸ºæ”¾å¤§å€æ•°ã€‚
æé«˜çµæ•度,å¯å¾—到较高的测é‡ç²¾åº¦ã€‚ä½†çµæ•度愈高,测é‡èŒƒå›´æ„ˆçª„,稳定性也往往愈差。
åˆ†è¾¨çŽ‡åˆ†è¾¨çŽ‡æ˜¯æŒ‡ä¼ æ„Ÿå™¨å¯æ„Ÿå—到的被测é‡çš„æœ€å°å˜åŒ–的能力。也就是说,如果输入é‡ä»ŽæŸä¸€éžé›¶å€¼ç¼“慢地å˜åŒ–。当输入å˜åŒ–值未超过æŸä¸€æ•°å€¼æ—¶ï¼Œä¼ 感器的输出ä¸ä¼šå‘生å˜åŒ–,å³ä¼ 感器对æ¤è¾“å…¥é‡çš„å˜åŒ–是分辨ä¸å‡ºæ¥çš„ã€‚åªæœ‰å½“输入é‡çš„å˜åŒ–超过分辨率时,其输出æ‰ä¼šå‘生å˜åŒ–。
é€šå¸¸ä¼ æ„Ÿå™¨åœ¨æ»¡é‡ç¨‹èŒƒå›´å†…å„点的分辨率并ä¸ç›¸åŒï¼Œå› æ¤å¸¸ç”¨æ»¡é‡ç¨‹ä¸èƒ½ä½¿è¾“出é‡äº§ç”Ÿé˜¶è·ƒå˜åŒ–的输入é‡ä¸çš„æœ€å¤§å˜åŒ–值作为衡é‡åˆ†è¾¨çŽ‡çš„æŒ‡æ ‡ã€‚ä¸Šè¿°æŒ‡æ ‡è‹¥ç”¨æ»¡é‡ç¨‹çš„ç™¾åˆ†æ¯”è¡¨ç¤ºï¼Œåˆ™ç§°ä¸ºåˆ†è¾¨çŽ‡ã€‚åˆ†è¾¨çŽ‡ä¸Žä¼ æ„Ÿå™¨çš„ç¨³å®šæ€§æœ‰è´Ÿç›¸ç›¸å…³æ€§ã€‚
8选型原则To carry out a specific measurement work, we must first consider the principle of the use of sensors, which need to analyze many factors before you can determine. Because, even if it is to measure the same physical quantity, there are many kinds of principle sensors available for selection. Which kind of principle sensor is more appropriate, we need to consider the following specific problems according to the characteristics of the measured and the use conditions of the sensor: the size of the range; The measured position of the sensor volume requirements; measurement method for contact or non-contact; signal extraction method, wired or non-contact measurement; sensor source, domestic or imported, the price can withstand, or self-developed.
After considering the above issues, it is possible to determine which type of sensor to use, and then consider the specific performance indicators of the sensor.
The choice of sensitivityGenerally, in the linear range of the sensor, it is desirable that the sensitivity of the sensor is as high as possible. Because only the sensitivity is high, the value of the output signal corresponding to the measured change is relatively large, which is advantageous for signal processing. However, it should be noted that the sensitivity of the sensor is high, and external noise that is not related to the measurement is easily mixed in, and it is also amplified by the amplification system, which affects the measurement accuracy.å› æ¤ï¼Œè¦æ±‚ä¼ æ„Ÿå™¨æœ¬èº«åº”å…·æœ‰è¾ƒé«˜çš„ä¿¡å™ªæ¯”ï¼Œå°½é‡å‡å°‘从外界引入的干扰信å·ã€‚
The sensitivity of the sensor is directional. When it is measured as a single vector and its directionality is higher, sensors with small sensitivity in other directions should be selected; if the measured is a multidimensional vector, the cross sensitivity of the sensor is required to be as small as possible.
频率å“åº”ç‰¹æ€§ä¼ æ„Ÿå™¨çš„é¢‘çŽ‡å“应特性决定了被测é‡çš„频率范围,必须在å…è®¸é¢‘çŽ‡èŒƒå›´å†…ä¿æŒä¸å¤±çœŸã€‚å®žé™…ä¸Šä¼ æ„Ÿå™¨çš„å“应总有—定延迟,希望延迟时间越çŸè¶Šå¥½ã€‚
ä¼ æ„Ÿå™¨çš„é¢‘çŽ‡å“åº”è¶Šé«˜ï¼Œå¯æµ‹çš„ä¿¡å·é¢‘率范围就越宽。
åœ¨åŠ¨æ€æµ‹é‡ä¸ï¼Œåº”æ ¹æ®ä¿¡å·çš„特点(稳æ€ã€çž¬æ€ã€éšæœºç‰ï¼‰å“应特性,以å…产生过大的误差。
Linear rangeThe linear range of the sensor refers to the range of the output proportional to the input. In theory, in this range, the sensitivity remains constant. The wider the linear range of the sensor, the larger the range, and can guarantee a certain measurement accuracy. When selecting a sensor, when the type of the sensor is determined, it first depends on whether or not the range satisfies the requirement.
But in fact, any sensor cannot guarantee absolute linearity, and its linearity is also relative. When the required measurement accuracy is relatively low, within a certain range, the sensor with smaller nonlinear error can be approximated as linear, which will bring great convenience to the measurement.
ç¨³å®šæ€§ä¼ æ„Ÿå™¨ä½¿ç”¨ä¸€æ®µæ—¶é—´åŽï¼Œå…¶æ€§èƒ½ä¿æŒä¸å˜çš„能力称为稳定性。影å“ä¼ æ„Ÿå™¨é•¿æœŸç¨³å®šæ€§çš„å› ç´ é™¤ä¼ æ„Ÿå™¨æœ¬èº«ç»“æž„å¤–ï¼Œä¸»è¦æ˜¯ä¼ æ„Ÿå™¨çš„ä½¿ç”¨çŽ¯å¢ƒã€‚å› æ¤ï¼Œè¦ä½¿ä¼ æ„Ÿå™¨å…·æœ‰è‰¯å¥½çš„ç¨³å®šæ€§ï¼Œä¼ æ„Ÿå™¨å¿…é¡»è¦æœ‰è¾ƒå¼ºçš„环境适应能力。
åœ¨é€‰æ‹©ä¼ æ„Ÿå™¨ä¹‹å‰ï¼Œåº”å¯¹å…¶ä½¿ç”¨çŽ¯å¢ƒè¿›è¡Œè°ƒæŸ¥ï¼Œå¹¶æ ¹æ®å…·ä½“的使用环境选择åˆé€‚çš„ä¼ æ„Ÿå™¨ï¼Œæˆ–é‡‡å–适当的措施,å‡å°çŽ¯å¢ƒçš„å½±å“。
ä¼ æ„Ÿå™¨çš„ç¨³å®šæ€§æœ‰å®šé‡æŒ‡æ ‡ï¼Œåœ¨è¶…过使用期åŽï¼Œåœ¨ä½¿ç”¨å‰åº”釿–°è¿›è¡Œæ ‡å®šï¼Œä»¥ç¡®å®šä¼ 感器的性能是å¦å‘生å˜åŒ–。
在æŸäº›è¦æ±‚ä¼ æ„Ÿå™¨èƒ½é•¿æœŸä½¿ç”¨è€Œåˆä¸èƒ½è½»æ˜“æ›´æ¢æˆ–æ ‡å®šçš„åœºåˆï¼Œæ‰€é€‰ç”¨çš„ä¼ æ„Ÿå™¨ç¨³å®šæ€§è¦æ±‚æ›´ä¸¥æ ¼ï¼Œè¦èƒ½å¤Ÿç»å—ä½é•¿æ—¶é—´çš„考验。
ç²¾åº¦ç²¾åº¦æ˜¯ä¼ æ„Ÿå™¨çš„ä¸€ä¸ªé‡è¦çš„æ€§èƒ½æŒ‡æ ‡ï¼Œå®ƒæ˜¯å…³ç³»åˆ°æ•´ä¸ªæµ‹é‡ç³»ç»Ÿæµ‹é‡ç²¾åº¦çš„一个é‡è¦çŽ¯èŠ‚ã€‚ä¼ æ„Ÿå™¨çš„ç²¾åº¦è¶Šé«˜ï¼Œå…¶ä»·æ ¼è¶Šæ˜‚è´µï¼Œå› æ¤ï¼Œä¼ 感器的精度åªè¦æ»¡è¶³æ•´ä¸ªæµ‹é‡ç³»ç»Ÿçš„ç²¾åº¦è¦æ±‚å°±å¯ä»¥ï¼Œä¸å¿…é€‰å¾—è¿‡é«˜ã€‚è¿™æ ·å°±å¯ä»¥åœ¨æ»¡è¶³åŒä¸€æµ‹é‡ç›®çš„çš„è¯¸å¤šä¼ æ„Ÿå™¨ä¸é€‰æ‹©æ¯”较便宜和简å•çš„ä¼ æ„Ÿå™¨é˜¿ç‰¹æ‹‰æ–¯ç©ºåŽ‹æœºé…件。
如果测é‡ç›®çš„æ˜¯å®šæ€§åˆ†æžçš„,选用é‡å¤ç²¾åº¦é«˜çš„ä¼ æ„Ÿå™¨å³å¯ï¼Œä¸å®œé€‰ç”¨ç»å¯¹é‡å€¼ç²¾åº¦é«˜çš„;如果是为了定é‡åˆ†æžï¼Œå¿…须获得精确的测é‡å€¼ï¼Œå°±éœ€é€‰ç”¨ç²¾åº¦ç‰çº§èƒ½æ»¡è¶³è¦æ±‚çš„ä¼ æ„Ÿå™¨ã€‚
对æŸäº›ç‰¹æ®Šä½¿ç”¨åœºåˆï¼Œæ— 法选到åˆé€‚çš„ä¼ æ„Ÿå™¨ï¼Œåˆ™éœ€è‡ªè¡Œè®¾è®¡åˆ¶é€ ä¼ æ„Ÿå™¨ã€‚è‡ªåˆ¶ä¼ æ„Ÿå™¨çš„æ€§èƒ½åº”æ»¡è¶³ä½¿ç”¨è¦æ±‚。
9常用术è¯1ã€ä¼ 感器
能感å—规定的被测é‡å¹¶æŒ‰ç…§ä¸€å®šçš„è§„å¾‹è½¬æ¢æˆå¯ç”¨è¾“出信å·çš„å™¨ä»¶æˆ–è£…ç½®ã€‚é€šå¸¸æœ‰æ•æ„Ÿå…ƒä»¶å’Œè½¬æ¢å…ƒä»¶ç»„æˆã€‚
1ï¼‰æ•æ„Ÿå…ƒä»¶æ˜¯æŒ‡ä¼ 感器ä¸èƒ½ç›´æŽ¥ï¼ˆæˆ–å“应)被测é‡çš„部分。
2)转æ¢å…ƒä»¶æŒ‡ä¼ 感器ä¸èƒ½è¾ƒæ•感元件感å—(或å“应)的被测é‡è½¬æ¢æˆæ˜¯ä¸Žä¼ 输和(或)测é‡çš„电信å·éƒ¨åˆ†ã€‚
3ï¼‰å½“è¾“å‡ºä¸ºè§„å®šçš„æ ‡å‡†ä¿¡å·æ—¶ï¼Œåˆ™ç§°ä¸ºå˜é€å™¨ã€‚
2ã€æµ‹é‡èŒƒå›´
在å…许误差é™å†…被测é‡å€¼çš„范围。
3ã€é‡ç¨‹
测é‡èŒƒå›´ä¸Šé™å€¼å’Œä¸‹é™å€¼çš„代数差。
4ã€ç²¾ç¡®åº¦
被测é‡çš„æµ‹é‡ç»“果与真值间的一致程度。
5ã€é‡å¤æ€§
在所有下述æ¡ä»¶ä¸‹ï¼Œå¯¹åŒä¸€è¢«æµ‹çš„é‡è¿›è¡Œå¤šæ¬¡è¿žç»æµ‹é‡æ‰€å¾—结果之间的符åˆç¨‹åº¦ï¼š
ç›¸åŒæµ‹é‡æ–¹æ³•
相åŒè§‚测者
ç›¸åŒæµ‹é‡ä»ªå™¨
相åŒåœ°ç‚¹
相åŒä½¿ç”¨æ¡ä»¶
åœ¨çŸæ—¶æœŸå†…çš„é‡å¤ã€‚
6ã€åˆ†è¾¨åŠ›
ä¼ æ„Ÿå™¨åœ¨è§„å®šæµ‹é‡èŒƒå›´å†…å¯èƒ½æ£€æµ‹å‡ºçš„被测é‡çš„æœ€å°å˜åŒ–é‡ã€‚
7ã€é˜ˆå€¼
èƒ½ä½¿ä¼ æ„Ÿå™¨è¾“å‡ºç«¯äº§ç”Ÿå¯æµ‹å˜åŒ–é‡çš„被测é‡çš„æœ€å°å˜åŒ–é‡ã€‚
8ã€é›¶ä½
使输出的ç»å¯¹å€¼ä¸ºæœ€å°çš„状æ€ï¼Œä¾‹å¦‚平衡状æ€ã€‚
9ã€æ¿€åб
ä¸ºä½¿ä¼ æ„Ÿå™¨æ£å¸¸å·¥ä½œè€Œæ–½åŠ çš„å¤–éƒ¨èƒ½é‡ï¼ˆç”µåŽ‹æˆ–ç”µæµï¼‰ã€‚
10ã€æœ€å¤§æ¿€åб
在市内æ¡ä»¶ä¸‹ï¼Œèƒ½å¤Ÿæ–½åŠ åˆ°ä¼ æ„Ÿå™¨ä¸Šçš„æ¿€åŠ±ç”µåŽ‹æˆ–ç”µæµçš„æœ€å¤§å€¼ã€‚
11ã€è¾“入阻抗
在输出端çŸè·¯æ—¶ï¼Œä¼ 感器输入端测得的阻抗。
12ã€è¾“出
æœ‰ä¼ æ„Ÿå™¨äº§ç”Ÿçš„ä¸Žå¤–åŠ è¢«æµ‹é‡æˆå‡½æ•°å…³ç³»çš„电é‡ã€‚
13ã€è¾“出阻抗
在输入端çŸè·¯æ—¶ï¼Œä¼ 感器输出端测得的阻抗。
14ã€é›¶ç‚¹è¾“出
在室内æ¡ä»¶ä¸‹ï¼Œæ‰€åŠ è¢«æµ‹é‡ä¸ºé›¶æ—¶ä¼ 感器的输出。
15ã€æ»žåŽ
在规定的范围内,当被测é‡å€¼å¢žåŠ å’Œå‡å°‘时,输出ä¸å‡ºçŽ°çš„æœ€å¤§å·®å€¼ã€‚
16ã€è¿ŸåŽ
输出信å·å˜åŒ–相对于输入信å·å˜åŒ–的时间延迟。
17ã€æ¼‚ç§»
åœ¨ä¸€å®šçš„æ—¶é—´é—´éš”å†…ï¼Œä¼ æ„Ÿå™¨è¾“å‡ºä¸æœ‰ä¸Žè¢«æµ‹é‡æ— 关的ä¸éœ€è¦çš„å˜åŒ–é‡ã€‚
18ã€é›¶ç‚¹æ¼‚ç§»
在规定的时间间隔åŠå®¤å†…æ¡ä»¶ä¸‹é›¶ç‚¹è¾“出时的å˜åŒ–。
19ã€çµæ•度
ä¼ æ„Ÿå™¨è¾“å‡ºé‡çš„增é‡ä¸Žç›¸åº”的输入é‡å¢žé‡ä¹‹æ¯”。
20ã€çµæ•度漂移
ç”±äºŽçµæ•度的å˜åŒ–è€Œå¼•èµ·çš„æ ¡å‡†æ›²çº¿æ–œçŽ‡çš„å˜åŒ–。
21ã€çƒçµæ•度漂移
ç”±äºŽçµæ•度的å˜åŒ–è€Œå¼•èµ·çš„çµæ•度漂移。
22ã€çƒé›¶ç‚¹æ¼‚ç§»
由于周围温度å˜åŒ–而引起的零点漂移。
23ã€çº¿æ€§åº¦
æ ¡å‡†æ›²çº¿ä¸ŽæŸä¸€è§„定直线一致的程度。
24ã€éžçº¿æ€§åº¦
æ ¡å‡†æ›²çº¿ä¸ŽæŸä¸€è§„定直线å离的程度。
25ã€é•¿æœŸç¨³å®šæ€§
ä¼ æ„Ÿå™¨åœ¨è§„å®šçš„æ—¶é—´å†…ä»èƒ½ä¿æŒä¸è¶…过å…许误差的能力。
26ã€å›ºæœ‰é¢‘率
åœ¨æ— é˜»åŠ›æ—¶ï¼Œä¼ æ„Ÿå™¨çš„è‡ªç”±ï¼ˆä¸åŠ å¤–åŠ›ï¼‰æŒ¯è¡é¢‘率。
27ã€å“应
输出时被测é‡å˜åŒ–的特性。
28ã€è¡¥å¿æ¸©åº¦èŒƒå›´
ä½¿ä¼ æ„Ÿå™¨ä¿æŒé‡ç¨‹å’Œè§„定æžé™å†…的零平衡所补å¿çš„æ¸©åº¦èŒƒå›´ã€‚
29ã€è •å˜
å½“è¢«æµ‹é‡æœºå™¨å¤šæœ‰çŽ¯å¢ƒæ¡ä»¶ä¿æŒæ’定时,在规定时间内输出é‡çš„å˜åŒ–。
30ã€ç»ç¼˜ç”µé˜»
å¦‚æ— å…¶ä»–è§„å®šï¼ŒæŒ‡åœ¨å®¤æ¸©æ¡ä»¶ä¸‹æ–½åŠ è§„å®šçš„ç›´æµç”µåŽ‹æ—¶ï¼Œä»Žä¼ æ„Ÿå™¨è§„å®šç»ç¼˜éƒ¨åˆ†ä¹‹é—´æµ‹å¾—的电阻值。
10环境影å“çŽ¯å¢ƒç»™ä¼ æ„Ÿå™¨é€ æˆçš„å½±å“ä¸»è¦æœ‰ä»¥ä¸‹å‡ 个方é¢ï¼š
(1ï¼‰é«˜æ¸©çŽ¯å¢ƒå¯¹ä¼ æ„Ÿå™¨é€ æˆæ¶‚è¦†ææ–™ç†”化ã€ç„Šç‚¹å¼€åŒ–ã€å¼¹æ€§ä½“内应力å‘生结构å˜åŒ–ç‰é—®é¢˜ã€‚å¯¹äºŽé«˜æ¸©çŽ¯å¢ƒä¸‹å·¥ä½œçš„ä¼ æ„Ÿå™¨å¸¸é‡‡ç”¨è€é«˜æ¸©ä¼ 感器;å¦å¤–ï¼Œå¿…é¡»åŠ æœ‰éš”çƒã€æ°´å†·æˆ–气冷ç‰è£…置。
(2ï¼‰ç²‰å°˜ã€æ½®æ¹¿å¯¹ä¼ æ„Ÿå™¨é€ æˆçŸè·¯çš„å½±å“。在æ¤çŽ¯å¢ƒæ¡ä»¶ä¸‹åº”é€‰ç”¨å¯†é—æ€§å¾ˆé«˜çš„ä¼ æ„Ÿå™¨ã€‚ä¸åŒçš„ä¼ æ„Ÿå™¨å…¶å¯†å°çš„æ–¹å¼æ˜¯ä¸åŒçš„ï¼Œå…¶å¯†é—æ€§å˜åœ¨ç€å¾ˆå¤§å·®å¼‚。
常è§çš„坆尿œ‰å¯†å°èƒ¶å……填或涂覆;橡胶垫机械紧固密å°ï¼›ç„ŠæŽ¥ï¼ˆæ°©å¼§ç„Šã€ç‰ç¦»åæŸç„Šï¼‰å’ŒæŠ½çœŸç©ºå……氮密å°ã€‚
ä»Žå¯†å°æ•ˆæžœæ¥çœ‹ï¼Œç„пޥ坆å°ä¸ºæœ€ä½³ï¼Œå……填涂覆密å°èƒ¶ä¸ºæœ€å·®ã€‚对于室内干净ã€å¹²ç‡¥çŽ¯å¢ƒä¸‹å·¥ä½œçš„ä¼ æ„Ÿå™¨ï¼Œå¯é€‰æ‹©æ¶‚胶密å°çš„ä¼ æ„Ÿå™¨ï¼Œè€Œå¯¹äºŽä¸€äº›åœ¨æ½®æ¹¿ã€ç²‰å°˜æ€§è¾ƒé«˜çš„çŽ¯å¢ƒä¸‹å·¥ä½œçš„ä¼ æ„Ÿå™¨ï¼Œåº”é€‰æ‹©è†œç‰‡çƒå¥—坆尿ˆ–膜片焊接密å°ã€æŠ½çœŸç©ºå……æ°®çš„ä¼ æ„Ÿå™¨ã€‚
(3)在è…蚀性较高的环境下,如潮湿ã€é…¸æ€§å¯¹ä¼ æ„Ÿå™¨é€ æˆå¼¹æ€§ä½“å—æŸæˆ–产生çŸè·¯ç‰å½±å“,应选择外表é¢è¿›è¡Œè¿‡å–·å¡‘或ä¸é”ˆé’¢å¤–罩,抗è…èš€æ€§èƒ½å¥½ä¸”å¯†é—æ€§å¥½çš„ä¼ æ„Ÿå™¨ã€‚
(4)电ç£åœºå¯¹ä¼ 感器输出紊乱信å·çš„å½±å“ã€‚åœ¨æ¤æƒ…å†µä¸‹ï¼Œåº”å¯¹ä¼ æ„Ÿå™¨çš„å±è”½æ€§è¿›è¡Œä¸¥æ ¼æ£€æŸ¥ï¼Œçœ‹å…¶æ˜¯å¦å…·æœ‰è‰¯å¥½çš„æŠ—电ç£èƒ½åŠ›ã€‚
(5ï¼‰æ˜“ç‡ƒã€æ˜“爆ä¸ä»…å¯¹ä¼ æ„Ÿå™¨é€ æˆå½»åº•性的æŸå®³ï¼Œè€Œä¸”è¿˜ç»™å…¶å®ƒè®¾å¤‡å’Œäººèº«å®‰å…¨é€ æˆå¾ˆå¤§çš„å¨èƒã€‚å› æ¤ï¼Œåœ¨æ˜“ç‡ƒã€æ˜“çˆ†çŽ¯å¢ƒä¸‹å·¥ä½œçš„ä¼ æ„Ÿå™¨å¯¹é˜²çˆ†æ€§èƒ½æå‡ºäº†æ›´é«˜çš„è¦æ±‚ï¼šåœ¨æ˜“ç‡ƒã€æ˜“çˆ†çŽ¯å¢ƒä¸‹å¿…é¡»é€‰ç”¨é˜²çˆ†ä¼ æ„Ÿå™¨ï¼Œè¿™ç§ä¼ 感器的密å°å¤–罩ä¸ä»…è¦è€ƒè™‘其坆闿€§ï¼Œè¿˜è¦è€ƒè™‘到防爆强度,以åŠç”µç¼†çº¿å¼•出头的防水ã€é˜²æ½®ã€é˜²çˆ†æ€§ç‰ã€‚
11é€‰æ‹©ä½¿ç”¨å¯¹ä¼ æ„Ÿå™¨æ•°é‡å’Œé‡ç¨‹çš„选择:
ä¼ æ„Ÿå™¨æ•°é‡çš„é€‰æ‹©æ˜¯æ ¹æ®ç”µå衡器的用途ã€ç§¤ä½“éœ€è¦æ”¯æ’‘çš„ç‚¹æ•°ï¼ˆæ”¯æ’‘ç‚¹æ•°åº”æ ¹æ®ä½¿ç§¤ä½“å‡ ä½•é‡å¿ƒå’Œå®žé™…é‡å¿ƒé‡åˆçš„原则而确定)而定。一般æ¥è¯´ï¼Œç§¤ä½“æœ‰å‡ ä¸ªæ”¯æ’‘ç‚¹å°±é€‰ç”¨å‡ åªä¼ 感器,但是对于一些特殊的秤体如电ååŠé’©ç§¤å°±åªèƒ½é‡‡ç”¨ä¸€ä¸ªä¼ 感器,一些机电结åˆç§¤å°±åº”æ ¹æ®å®žé™…情况æ¥ç¡®å®šé€‰ç”¨ä¼ 感器的个数。
ä¼ æ„Ÿå™¨é‡ç¨‹çš„选择å¯ä¾æ®ç§¤çš„æœ€å¤§ç§°é‡å€¼ã€é€‰ç”¨ä¼ 感器的个数ã€ç§¤ä½“的自é‡ã€å¯èƒ½äº§ç”Ÿçš„æœ€å¤§åè½½åŠåŠ¨è½½ç‰å› ç´ ç»¼åˆè¯„ä»·æ¥ç¡®å®šã€‚一般æ¥è¯´ï¼Œä¼ 感器的é‡ç¨‹è¶ŠæŽ¥è¿‘分é…到æ¯ä¸ªä¼ 感器的载è·ï¼Œå…¶ç§°é‡çš„å‡†ç¡®åº¦å°±è¶Šé«˜ã€‚ä½†åœ¨å®žé™…ä½¿ç”¨æ—¶ï¼Œç”±äºŽåŠ åœ¨ä¼ æ„Ÿå™¨ä¸Šçš„è½½è·é™¤è¢«ç§°ç‰©ä½“外,还å˜åœ¨ç§¤ä½“自é‡ã€çš®é‡ã€åè½½åŠæŒ¯åЍ冲击ç‰è½½è·ï¼Œå› æ¤é€‰ç”¨ä¼ 感器é‡ç¨‹æ—¶ï¼Œè¦è€ƒè™‘诸多方é¢çš„å› ç´ ï¼Œä¿è¯ä¼ 感器的安全和寿命。
ä¼ æ„Ÿå™¨é‡ç¨‹çš„è®¡ç®—å…¬å¼æ˜¯åœ¨å……分考虑到影å“秤体的å„ä¸ªå› ç´ åŽï¼Œç»è¿‡å¤§é‡çš„实验而确定的。
å…¬å¼å¦‚下:
C=K-0K-1K-2K-3(Wmax+W)/N
C—å•ä¸ªä¼ æ„Ÿå™¨çš„é¢å®šé‡ç¨‹
W—秤体自é‡
Wmax—被称物体净é‡çš„æœ€å¤§å€¼
N—秤体所采用支撑点的数é‡
K-0—ä¿é™©ç³»æ•°ï¼Œä¸€èˆ¬å–值在1.2~1.3之间
K-1—冲击系数
K-2—秤体的é‡å¿ƒå移系数
K-3—风压系数
æ ¹æ®ç»éªŒï¼Œä¸€èˆ¬åº”ä½¿ä¼ æ„Ÿå™¨å·¥ä½œåœ¨å…¶30%~70%é‡ç¨‹å†…,但对于一些在使用过程ä¸å˜åœ¨è¾ƒå¤§å†²å‡»åŠ›çš„è¡¡å™¨ï¼Œå¦‚åŠ¨æ€è½¨é“è¡¡ã€åŠ¨æ€æ±½è½¦è¡¡ã€é’¢æç§¤ç‰ï¼Œåœ¨é€‰ç”¨ä¼ æ„Ÿå™¨æ—¶ï¼Œä¸€èˆ¬è¦æ‰©å¤§å…¶é‡ç¨‹ï¼Œä½¿ä¼ 感器工作在其é‡ç¨‹çš„20%~30%ä¹‹å†…ï¼Œä½¿ä¼ æ„Ÿå™¨çš„ç§°é‡å‚¨å¤‡é‡å¢žå¤§ï¼Œä»¥ä¿è¯ä¼ 感器的使用安全和寿命。
è¦è€ƒè™‘å„ç§ç±»åž‹ä¼ 感器的适用范围:
ä¼ æ„Ÿå™¨çš„å‡†ç¡®åº¦ç‰çº§åŒ…æ‹¬ä¼ æ„Ÿå™¨çš„éžçº¿å½¢ã€è •å˜ã€è •å˜æ¢å¤ã€æ»žåŽã€é‡å¤æ€§ã€çµæ•åº¦ç‰æŠ€æœ¯æŒ‡æ ‡ã€‚åœ¨é€‰ç”¨ä¼ æ„Ÿå™¨çš„æ—¶å€™ï¼Œä¸è¦å•纯追求高ç‰çº§çš„ä¼ æ„Ÿå™¨ï¼Œè€Œæ—¢è¦è€ƒè™‘满足电åç§¤çš„å‡†ç¡®åº¦è¦æ±‚,åˆè¦è€ƒè™‘å…¶æˆæœ¬ã€‚
å¯¹ä¼ æ„Ÿå™¨ç‰çº§çš„选择必须满足下列两个æ¡ä»¶ï¼š
1ã€æ»¡è¶³ä»ªè¡¨è¾“å…¥çš„è¦æ±‚ã€‚ç§°é‡æ˜¾ç¤ºä»ªè¡¨æ˜¯å¯¹ä¼ 感器的输出信å·ç»è¿‡æ”¾å¤§ã€A/D转æ¢ç‰å¤„ç†ä¹‹åŽæ˜¾ç¤ºç§°é‡ç»“æžœçš„ã€‚å› æ¤ï¼Œä¼ 感器的输出信å·å¿…须大于或ç‰äºŽä»ªè¡¨è¦æ±‚的输入信å·å¤§å°ï¼Œå³å°†ä¼ æ„Ÿå™¨çš„è¾“å‡ºçµæ•åº¦ä»£äººä¼ æ„Ÿå™¨å’Œä»ªè¡¨çš„åŒ¹é…å…¬å¼ï¼Œè®¡ç®—结果须大于或ç‰äºŽä»ªè¡¨è¦æ±‚çš„è¾“å…¥çµæ•度。
2ã€æ»¡è¶³æ•´å°ç”µåç§¤å‡†ç¡®åº¦çš„è¦æ±‚。一å°ç”µåç§¤ä¸»è¦æ˜¯ç”±ç§¤ä½“ã€ä¼ 感器ã€ä»ªè¡¨ä¸‰éƒ¨åˆ†ç»„æˆï¼Œåœ¨å¯¹ä¼ æ„Ÿå™¨å‡†ç¡®åº¦é€‰æ‹©çš„æ—¶å€™ï¼Œåº”ä½¿ä¼ æ„Ÿå™¨çš„å‡†ç¡®åº¦ç•¥é«˜äºŽç†è®ºè®¡ç®—å€¼ï¼Œå› ä¸ºç†è®ºå¾€å¾€å—到客观æ¡ä»¶çš„é™åˆ¶ï¼Œå¦‚ç§¤ä½“çš„å¼ºåº¦å·®ä¸€ç‚¹ï¼Œä»ªè¡¨çš„æ€§èƒ½ä¸æ˜¯å¾ˆå¥½ã€ç§¤çš„工作环境比较æ¶åŠ£ç‰å› ç´ éƒ½ç›´æŽ¥å½±å“åˆ°ç§¤çš„å‡†ç¡®åº¦è¦æ±‚ï¼Œå› æ¤è¦ä»Žå„æ–¹é¢æé«˜è¦æ±‚,åˆè¦è€ƒè™‘ç»æµŽæ•ˆç›Šï¼Œç¡®ä¿è¾¾åˆ°ç›®çš„。
12å›½å®¶æ ‡å‡†ä¸Žä¼ æ„Ÿå™¨ç›¸å…³çš„çŽ°è¡Œå›½å®¶æ ‡å‡†
GB/T 14479-1993 ä¼ æ„Ÿå™¨å›¾ç”¨å›¾å½¢ç¬¦å·
GB/T 15478-1995 åŽ‹åŠ›ä¼ æ„Ÿå™¨æ€§èƒ½è¯•éªŒæ–¹æ³•
GB/T 15768-1995 ç”µå®¹å¼æ¹¿æ•å…ƒä»¶ä¸Žæ¹¿åº¦ä¼ æ„Ÿå™¨æ€»è§„èŒƒ
GB/T 15865-1995 æ‘„åƒæœºï¼ˆPAL/SECAM/NTSCï¼‰æµ‹é‡æ–¹æ³•第1部分:éžå¹¿æ’å•ä¼ æ„Ÿå™¨æ‘„åƒæœº
GB/T 13823.17-1996 æŒ¯åŠ¨ä¸Žå†²å‡»ä¼ æ„Ÿå™¨çš„æ ¡å‡†æ–¹æ³•å£°çµæ•度测试
GB/T 18459-2001 ä¼ æ„Ÿå™¨ä¸»è¦é™æ€æ€§èƒ½æŒ‡æ ‡è®¡ç®—方法
GB/T 18806-2002 电阻应å˜å¼åŽ‹åŠ›ä¼ æ„Ÿå™¨æ€»è§„èŒƒ
GB/T 18858.2-2002 低压开关设备和控制设备控制器-设备接å£ï¼ˆCDI) 第2部分:æ‰§è¡Œå™¨ä¼ æ„Ÿå™¨æŽ¥å£ï¼ˆAS-i)
GB/T 18901.1-2002 å…‰çº¤ä¼ æ„Ÿå™¨ç¬¬1部分:总规范
GB/T 19801-2005 æ— æŸæ£€æµ‹å£°å‘射检测声å‘å°„ä¼ æ„Ÿå™¨çš„äºŒçº§æ ¡å‡†
GB/T 7665-2005 ä¼ æ„Ÿå™¨é€šç”¨æœ¯è¯
GB/T 7666-2005 ä¼ æ„Ÿå™¨å‘½åæ³•åŠä»£å·
GB/T 11349.1-2006 振动与冲击机械导纳的试验确定第1éƒ¨åˆ†ï¼šåŸºæœ¬å®šä¹‰ä¸Žä¼ æ„Ÿå™¨
GB/T 20521-2006 åŠå¯¼ä½“器件第14-1部分: åŠå¯¼ä½“ä¼ æ„Ÿå™¨-总则和分类
GB/T 14048.15-2006 低压开关设备和控制设备第5-6部分:控制电路电器和开关元件-æŽ¥è¿‘ä¼ æ„Ÿå™¨å’Œå¼€å…³æ”¾å¤§å™¨çš„DC接å£ï¼ˆNAMUR)
GB/T 20522-2006 åŠå¯¼ä½“器件第14-3部分: åŠå¯¼ä½“ä¼ æ„Ÿå™¨-åŽ‹åŠ›ä¼ æ„Ÿå™¨
GB/T 20485.11-2006 æŒ¯åŠ¨ä¸Žå†²å‡»ä¼ æ„Ÿå™¨æ ¡å‡†æ–¹æ³•ç¬¬11部分:激光干涉法振动ç»å¯¹æ ¡å‡†
GB/T 20339-2006 å†œä¸šæ‹–æ‹‰æœºå’Œæœºæ¢°å›ºå®šåœ¨æ‹–æ‹‰æœºä¸Šçš„ä¼ æ„Ÿå™¨è”æŽ¥è£…ç½®æŠ€æœ¯è§„èŒƒ
GB/T 20485.21-2007 æŒ¯åŠ¨ä¸Žå†²å‡»ä¼ æ„Ÿå™¨æ ¡å‡†æ–¹æ³•ç¬¬21éƒ¨åˆ†ï¼šæŒ¯åŠ¨æ¯”è¾ƒæ³•æ ¡å‡†
GB/T 20485.13-2007 æŒ¯åŠ¨ä¸Žå†²å‡»ä¼ æ„Ÿå™¨æ ¡å‡†æ–¹æ³•ç¬¬13部分: 激光干涉法冲击ç»å¯¹æ ¡å‡†
GB/T 13606-2007 土工试验仪器岩土工程仪器振弦å¼ä¼ 感
Custom Printing,Air Layer Fabric,Drill Rayon Fabric,Rayon Printed Fabric
Shaoxing MingFang Textile Co., Ltd , https://www.printings-fabric.com