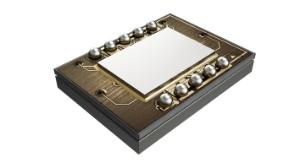
First, low g accelerometer sensing accuracy is limited In the terminal applications, low-g accelerometer MEMS products, in response to the basic type of motion sensing can get good use of benefits, but in fact, low g value of the accelerometer In the component performance, sensing accuracy has a certain degree of limit, if the user wants to get a more accurate somatosensory operation experience, due to the sensor's response to the reaction, and relatively limited somatosensory application design details.
Similarly, linear accelerometer MEMS, in fact, in the limited capacity of the chip sensing architecture design, and its performance in higher-precision applications show limitations, especially in human-machine interface applications and interactive design programs. At present, the optimal design is to use a Gyrosensor component supporting a multi-axis MEMS and a geomagnetic sensor reference to perform a high-precision dynamic sensing design.
Second, somatosensory gaming applications MEMS gyroscopes using heating so-called gyroscopes, in short, can be measured along one axis, or multi-axis angular velocity dynamic data movement, basically the use of gyros to supplement MEMS accelerometers Design solutions and auxiliary enhancement components that improve dynamic sensing accuracy, through real-time reference of acceleration sensing and angular velocity, can allow the operating system to obtain more accurate motion sensing data.
Gyroscope solutions use more and more components and the cost of parts continues to drop. For example, Nintendo launched the WiiMotionPlus controller joystick in 2009, using an additional MEMS gyroscope design solution to enhance the sensory accuracy of the original somatosensory game controller, and MotionPlus to detect the 3D angular velocity variation of the somatosensory joystick. Gaming machine import MEMS gyroscope sales growth nearly 3 times!
Another smart phone product is also keeping pace with the use of MEMS gyroscopes. The iPhone4 is the world’s first smart phone with built-in MEMS gyroscopes, and suppliers of MEMS gyroscopes for smart phone applications include STMicroelectronics, InvenSense, and Analog Devices.
MEMS gyroscopes are widely used in digital camera's electronic anti-shock design, laptop's hard drive drop protection, 3D space mouse, digital electronic compass, automotive ESC/ESP system design, or with automatic control system. Robotic control arm dynamic balance design scheme.
Third, the accelerometer integrates the gyroscope to enhance the application value At present, most accelerometers and gyroscopes are usually integrated design to construct a complete motion track that can dynamically track and capture 3D space. Taking the existing MEMS gyroscope as an example, the MEMS gyroscope (aka Gyroscope) is also known as the angular velocity meter. Actually, the core components of the MEMS gyroscope are a group of micromachining mechanical assemblies that have undergone silicon processing. They are referenced to a set of silicon structures. Like the operation mechanism of the tuning fork mechanism, the angular velocity sensing of the application device is based on the alternating Coriolis force caused by mutually orthogonal vibration and rotation, and the vibrating object is suspended from the base by a flexible elastic structure. The MEMS gyroscope's overall dynamics system is integrated by the 2D elastic damping system. The Coriolis force generated by the vibration and rotation in the system transfers the angular velocity energy to the sensing mode, and the angular velocity is converted into the specific sensing structure. Straight displacement, through the MEMS structure and then obtain a variable amount of sensing information.
The biggest difference between the gyroscope and the accelerometer is that the gyroscope's measured data is more skew than the inclination, yaw and other dynamic information, but rather with the gravity, linear motion sensing data is more independent, gyroscopes in the detection of object level changes When it is more effective, it can't be as sensitive as the accelerometer to the moving or moving kinetic energy of the object. On the contrary, accelerometers can be highly effective in detecting the moving state of an object, but they cannot sense small changes in the angle of the object. Therefore, by integrating the accelerometer and the gyroscope, the dynamic sensing system can simultaneously provide sensing information of the straight speed and rotation data, so that the detection range of the dynamic sensing system is more comprehensive and complete.
In the energy-saving design of MEMS, when the system does not need to use dynamic sensing applications, MEMS can be used to close part of the function to achieve high efficiency and energy saving. For example, in a gyro design scheme, the gyroscope's transmission signal and regulation circuit can be divided into two parts: the motor drive part and the accelerometer sensor circuit. The motor drive part uses the principle of electrostatic drive to make the mechanical components After the oscillating/absorbing operation, the resonance effect required for the sensing process is generated. As for the sensing part, the capacitance variation of the measurement system is used to obtain the Coriolis force value change, and the weak displacement data generated on the corresponding sensing particle point is obtained. The angular rate change is converted to the corresponding analog signal (or digital signal) output of the change in the angular velocity.
Our company advantages:
1. we are honest and reliable, and we hope we could be long-term partners.
2. We are professional, because there are a good team of engineers and designers in our factory.
3. We always stick to provide our customers high quality goods, best service, and sincere attitude to all our business partners.
4. We will guide every customer that how does our machine works, and welcome you come to visit our factory.
Technical Parameters:
1. Weight: 1500kg
2. Planting method: Round wire
3. Production speed: 500 rpm
4. Planting peak: 65mm
5. Planting pore size: φ1.6-φ4.0
6. Storable procedures: 1000 models
7. X-axis travel: 400mm;
8. Y-axis travel: 320mm;
9. Z-axis travel: 160mm;
10. Air input pressure: 0.8MPa
11. Rated voltage frequency single phase: 220V, 50Hz
12. Machine power: 2.0kw
13. Machine dimensions: 1.14 meters long, 1.84 meters wide and 1.75 meters high
14. Packing size: 1.8 meters length, 2.1 meters width, 2.1 meters height (conforming to standard container requirements).
More details, please contact us as soon as possible.
5 Axes 3 Heads Drill And Tuft Brush Machine
5 Axis 3 Heads Brush Machine,Brush Drilling And Tufting Machine,Drilling and Tufting Super Brush Machine,Broom Brush Tufting Making Machine
Yangzhou Blue State Digital Control Brush Equipment Co., LTD. , http://www.lbbrushmachine.com