I. Introduction
In sheet metal processing and manufacturing, choosing the right machinery is crucial for efficiency, productivity and product quality.  Machinery is widely used including shearing machines, flame-cutting, plasma cutting, laser cutting equipment, etc.
Two prominent sheet metal processing technologies in this field are hydraulic shearing machines and laser cutting machines. While both are integral to cutting and shaping metal, they each have distinct advantages and disadvantages.
One of the significant advantages of shearing machines is their ability to quickly process materials. Understanding the capabilities and limitations of both shearing machines and laser cutting technology allows businesses to optimize their production processes, reduce costs, and increase productivity.
It's essential to conduct a comparative analysis of hydraulic shearing machines vs. laser cutting machines, including cost, precision, material versatility, speed and efficiency, maintenance and operational costs, automation and ease of use, environmental impact, and long-term sustainability, to understand their respective strengths and weaknesses across various operational contexts.
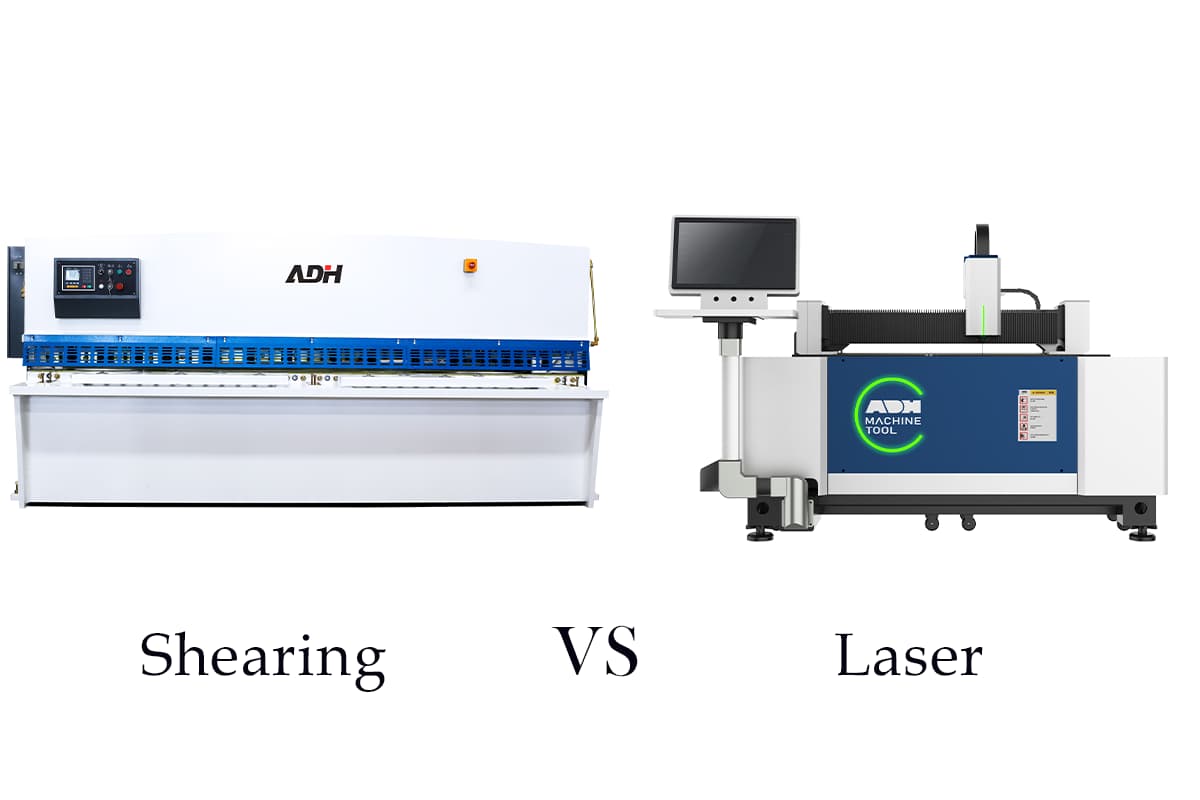
II. Hydraulic Shearing Machines vs. Laser Cutting Machines Analysis
Cutting Capabilities Matrix
Thickness Range | 0.5-40mm | 0.5-25mm |
Cutting Speed | 8-22 strokes/min | Up to 20m/min |
Precision | ±0.1mm | ±0.05mm |
Power Requirements | 5.5-7.5 KW | 500W-20kW |
Cost Comparison
Initial Investment
Hydraulic Shearing Machines:
- Generally lower initial investment, making them more accessible for small to medium-sized enterprises.
- Example: A small manufacturing business reported a 20% reduction in production costs due to the lower initial investment and operational expenses of hydraulic shearing machines.
Laser Cutting Machines:
- Significantly higher initial investment due to advanced technology and precision engineering.
- Example: An electronics manufacturer observed a substantial increase in their capital expenditure after adopting laser cutting technology.
Operational Costs
Hydraulic Shearing Machines:
- Lower energy consumption and simpler maintenance contribute to reduced ongoing costs.
- Example: A mid-sized manufacturing plant reduced maintenance downtime by 15% after implementing hydraulic shearing machines.
Laser Cutting Machines:
- Higher energy consumption and maintenance requirements can increase overall costs.
- Example: An automotive parts manufacturer reported higher-than-expected maintenance costs for their CO2 laser cutting machines.
Precision and Accuracy
Hydraulic Shearing Machines:
- Less precise, suitable for applications where intricate details are not critical.
- Case Study: Hydraulic shearing machines were unsuitable for a manufacturer of electronic components that are prone to wear and tear requiring precise circuit board patterns.
Laser Cutting Machines:
- Exceptional cutting precision and high cutting accuracy, capable of achieving tight tolerances and intricate designs.
- Kerf size - the width of the cut, which is minimal in laser cutting due to the focused beam.
- Case Study: A medical device manufacturer achieved tolerances as precise as ±0.05 mm, crucial for producing intricate components.
Material Versatility
Hydraulic Shearing Machines:
- Primarily designed for cutting metal sheets and plates, less effective with non-metallic materials or very thin sheets.
- Case Study: A custom fabrication shop found hydraulic shearing machines ineffective for cutting plastic sheets.
Laser Cutting Machines:
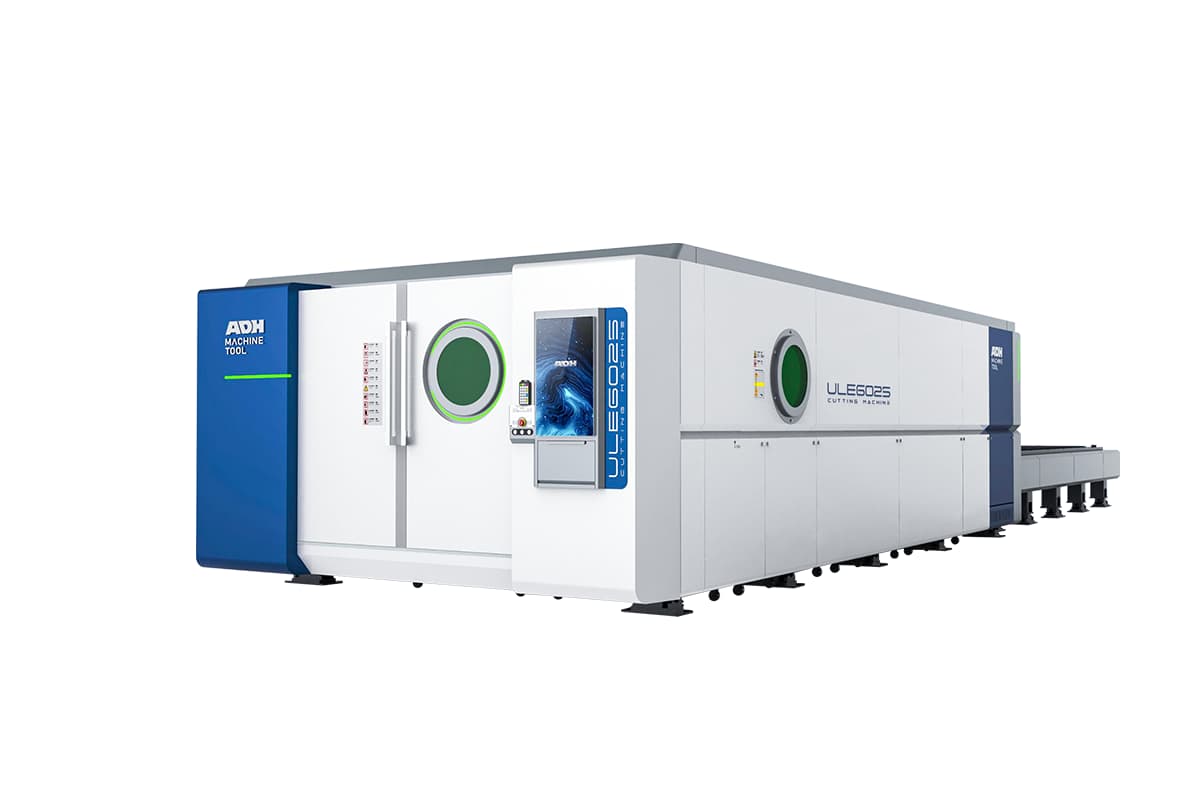
- Ability to cut a wide range of materials, including metals, plastics, wood, and composites.
- Case Study: An electronics manufacturer utilized laser cutting to produce small, intricate parts for circuit boards and connectors.
Speed and Efficiency
Hydraulic Shearing Machines:
- High-speed cutting for thick metal sheets, making them ideal for high-volume production.
- Case Study: An automotive parts manufacturer improved production line efficiency by 25% using hydraulic shearing machines for thick steel sheets.
Laser Cutting Machines:
- High speed for thin materials, but slower for thick materials compared to hydraulic shearing.
- Case Study: A fashion industry company reported a 30% increase in production speed for cutting fabric patterns using laser cutting machines.
Maintenance and Operational Costs
Hydraulic Shearing Machines:
- Simpler and less frequent maintenance due to fewer moving parts.
- Example: A mid-sized manufacturing plant reduced maintenance downtime by 15% after implementing hydraulic shearing machines.
Laser Cutting Machines:
- Higher maintenance requirements due to the complexity of the laser system and the need for regular replacement of parts such as gas tubes and optics.
- Example: An automotive parts manufacturer reported higher-than-expected maintenance costs for their CO2 laser cutting machines.
Automation and Ease of Use
Hydraulic Shearing Machines:
- Straightforward operation, suitable for operators with limited technical expertise.
- Limited automation capabilities compared to laser cutting machines.
- Example: A small workshop optimized space with compact hydraulic shearing machines, easily integrated into their existing production line.
Laser Cutting Machines:
- Highly automated, easily integrated with CAD/CAM systems for seamless design and manufacturing processes.
- Laser cutting machines require skilled operators but offers extensive automation capabilities.
- Example: An automotive parts manufacturer integrated laser cutting machines with CAD/CAM systems, resulting in a 20% increase in production efficiency.
Environmental Impact and Long-Term Sustainability
Hydraulic Shearing Machines:
- Lower energy consumption, contributing to a smaller carbon footprint.
- Minimal waste production as they typically produce fewer by-products during cutting.
- Example: A metal fabrication company reduced its carbon footprint by 15% by opting for hydraulic shearing machines.
Laser Cutting Machines:
- Higher energy consumption, which can lead to a larger carbon footprint.
- Can produce fumes and require proper ventilation systems to manage emissions.
- Example: An electronics manufacturer installed advanced filtration systems to mitigate the environmental impact of laser cutting fumes.
Innovative Applications and Emerging Trends
Hydraulic Shearing Machines:
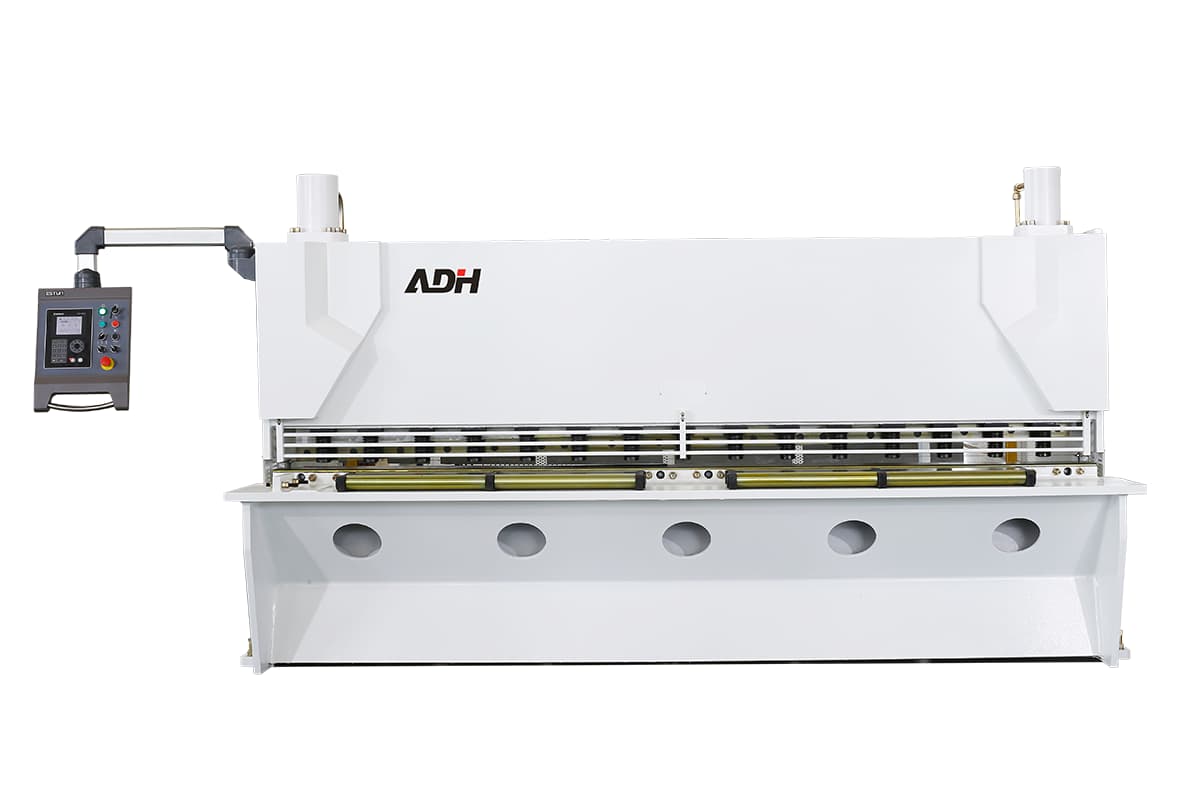
- Innovations in automation and CNC integration are making hydraulic shearing machines more versatile.
- Emerging trends include the use of hydraulic shearing in recycling and waste management for cutting scrap metal efficiently.
- Example: A recycling plant implemented automated hydraulic shearing machines to improve the efficiency of metal scrap processing.
Laser Cutting Machines:
- Advancements in fiber laser technology are enhancing fast cutting speed and precision, making lasers more accessible for various applications.
- Emerging trends include the use of laser cutting in additive manufacturing processes and hybrid systems combining laser cutting with other machining technologies.
- Example: A manufacturing company integrated laser cutting with 3D printing to create complex parts with high precision.
III. Hydraulic Shearing Machines vs. Laser Cutting Machines Comparison Table
Aspect | Hydraulic Shearing Machines | Laser Cutting Machines |
Types | Guillotine shearing machines; Swing beam shearing machines | CO2 laser cutting machines; Fiber laser cutting machines; Nd: YAG laser cutting machines |
Working Principle | The utilization of hydraulic power to exert substantial pressure to achieve the cutting process | Uses a high-powered laser beam focused into a small spot to melt, burn, or vaporize material. |
Cost | Lower initial investment and operational costs. | High upfront costs for purchase, installation, and training. |
Operation & Maintenance | Simple to operate with low maintenance requirements. | Requires skilled operators and frequent maintenance, especially for COâ‚‚ lasers. |
Cutting Speed | Fast for thick sheet metal sheets. | High-speed cutting, especially for thin materials. |
Precision | Lower precision; not suitable for intricate designs. | Extremely high precision with minimal kerf width. |
Material Versatility | Best suited for metal sheets; struggles with non-metallic materials or very thick metals. | Can cut various materials, including metals, plastics, wood, and fabrics. |
Material Deformation | Cutting may cause burrs, warping, or imperfections, requiring post-processing. | Minimal material deformation with smooth edges and minimal finishing required. |
Energy Efficiency | More energy-efficient with lower power consumption. | Higher energy consumption, particularly for COâ‚‚ lasers. |
Noise & Heat Generation | Generates noise and heat, requiring cooling and noise reduction systems. | Generally quieter but still requires fume extraction systems for certain materials. |
Environmental Impact | Uses hydraulic oil, which requires proper disposal; otherwise environmentally friendly. | Produces minimal waste, but cutting certain plastics may emit harmful gases. |
Safety | Advanced safety features (emergency stops, guards) but requires adherence to safety protocols. | Fume extraction and safety protocols are essential; exposure to the laser beam is hazardous. |
Cutting Capability | Limited to 2D cutting of metal sheets. | Can handle both 2D and limited 3D applications but not as well as waterjet cutters. |
Footprint and Size | Compact design makes it easier to integrate into production lines. | Larger machines with limited bed sizes for cutting large materials. |
Automation & Integration | Basic automation available. | Easily integrated with CAD/CAM systems for automated design and manufacturing. |
Tooling Costs | Requires physical tools but has lower replacement costs. | No tooling costs due to the contactless nature of laser cutting. |
Long-Term Costs | Lower operational costs over time. | Higher maintenance and operational costs accumulate over time. |
IV. Industry-Specific Applications
Automotive Industry
Hydraulic Shearing Machines
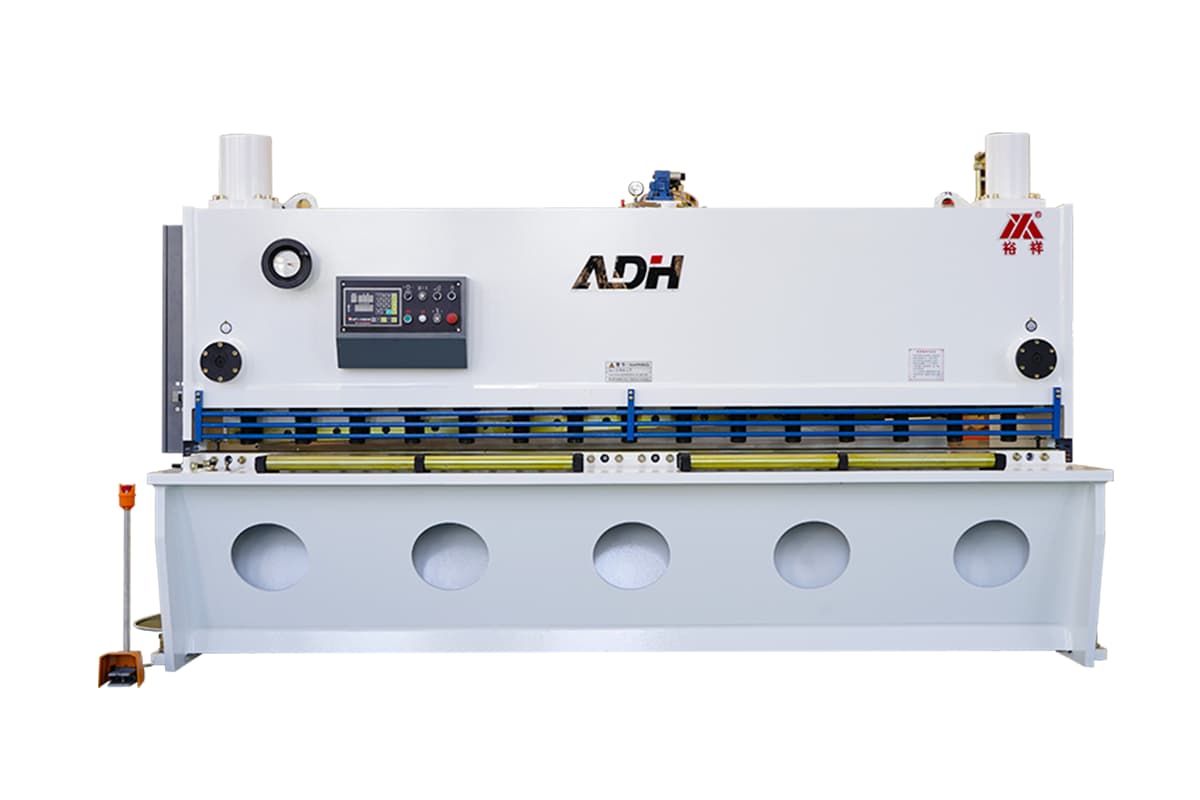
Hydraulic shearing machines are frequently used for cutting large metal sheets to manufacture car body parts, chassis, and other structural components. Their high-speed cutting capabilities make them ideal for processing the thick metal sheets often required in automotive manufacturing.
Laser Cutting Machines
Laser cutting machines excel in producing intricate and precise components required for modern vehicles. They are used for cutting and shaping metal parts, including body panels, engine components, and interior features. The precision and minimal material wastage offered by laser cutting are particularly beneficial for creating complex and lightweight automotive parts.
Aerospace Industry
Hydraulic Shearing Machines
Hydraulic shearing machines are used for cutting large sections of metal, such as aluminum and titanium sheets, used in constructing aircraft bodies and structural components. Their ability to handle thick materials efficiently makes them suitable for these heavy-duty applications.
Laser Cutting Machines
Laser cutting machines provide high precision and can be used to cut a wide range of materials, including metals, composites, and reflective materials. They are used for producing high-precision components such as turbine blades, aircraft skins, and intricate structural parts.
Construction Industry
Hydraulic Shearing Machines
In the construction industry, hydraulic shearing machines are employed for cutting metal components used in building projects, such as steel beams, metal sheets, and rebar. Their robust construction and high-speed cutting capabilities make them ideal for processing large volumes of construction materials efficiently.
Laser Cutting Machines
Laser cutting machines are used for creating detailed metal components, decorative elements, and customized architectural features. The precision and versatility of laser cutting allow for the production of intricate designs and high-quality finishes.
Electronics Industry
Hydraulic Shearing Machines
While less common in the electronics industry due to their limited precision, hydraulic shearing machines can still be used for cutting metal enclosures and larger components that do not require intricate detailing.
Laser Cutting Machines
Laser cutting machines are highly valued in the electronics industry for their ability to produce small, intricate parts with high precision. They are used for cutting circuit boards, connectors, and various electronic components, ensuring accuracy and minimal material wastage.
Custom Manufacturing
Hydraulic Shearing Machines
In custom manufacturing, hydraulic shearing machines are used for cutting a variety of metal materials to specific sizes and shapes. Their versatility and power make them suitable for handling diverse projects, from industrial machinery parts to unique architectural elements.
Laser Cutting Machines

Custom manufacturing greatly benefits from laser cutting machines due to their ability to produce detailed and complex designs. They are used for creating customized products, prototypes, and artistic pieces with high precision and quality.
V. Frequently Asked Questions
1. What are the main differences between hydraulic shearing machines and laser cutting machines?
Hydraulic shearing machines play a pivotal role in the metal fabrication industry, allowing for precise cutting of material, using a hydraulic system to exert shear force on a blade, and performing a guillotine-like shearing action on the metal. They are cost-effective and suitable for high-speed cutting of thick metal sheets but lack the precision and versatility of laser cutting machines.
In contrast, laser cutting machines utilize a high-powered laser beam, directed by CNC (Computer Numerical Control) systems, to make highly precise cuts in various materials. These cutting tools ideal for intricate designs and provide minimal material wastage but come with higher initial and operational costs. Additionally, laser cutting is a non-contact process, which reduces the risk of material contamination and tool wear.
Comparison Table:
Feature | Hydraulic Shearing Machine | Laser Cutting Machine |
Initial Cost | Lower | Higher |
Precision | Moderate | High |
Material Versatility | Primarily metal sheets | Various materials including metals, plastics, wood |
Thickness Capability | Suitable for thick materials | Limited effectiveness on very thick materials (>25mm) |
Speed | High for thick materials | Varies; slower for intricate cuts |
Maintenance | Simpler | More complex |
Operational Cost | Lower | Higher |
Applications | Automotive, construction, shipbuilding | Electronics, aerospace, custom fabrication |
2. Which machine is more cost-effective for small-scale operations?
Hydraulic shearing machines are generally more cost-effective for small-scale operations due to their lower initial investment and simpler maintenance requirements. They are ideal for businesses that primarily need to cut thick metal sheets and do not require the high precision offered by laser cutting machines.
3. Can laser cutting machines cut all types of materials?
While laser cutting machines are highly versatile and can cut a wide range of materials, including metals, plastics, wood, and composites, they are not suitable for all materials. Highly reflective materials, such as copper and aluminum, can be challenging, and very thick materials (typically beyond 25 mm) may not be efficiently cut by lasers. Specialized techniques and higher power settings can mitigate some of these limitations.
4. What kind of maintenance is required for hydraulic shearing machines?
Hydraulic shearing machines require regular maintenance to ensure optimal performance. Maintenance tasks include:
- Checking and replacing hydraulic oil
- Inspecting filters
- Ensuring hydraulic components function correctly
- Daily checks and proper lubrication
- Periodic servicing of the hydraulic system
Regular maintenance prevents mechanical failures and extends the machine's lifespan.
5. How does the precision of laser cutting compare to hydraulic shearing?
Laser cutting machines are significantly more precise than hydraulic shearing machines. They can achieve intricate designs with tight tolerances and minimal kerf sizes, making them suitable for applications requiring high sheet metal cutting accuracy. Hydraulic shearing machines, while effective for straightforward cuts, lack the precision needed for detailed and complex shapes.
6. Are there any safety concerns associated with using laser cutting machines?
Yes, laser cutting machines can pose safety concerns if not properly managed:
- The laser cutting process can produce harmful fumes and gases, necessitating proper ventilation and fume extraction systems.
- Direct contact with the laser beam can cause severe burns, so stringent safety protocols and protective equipment are essential.
- Regular safety training for operators is crucial to mitigate risks.
7. What are the typical applications of hydraulic shearing machines in the industry?
Hydraulic shearing machines are typically used in:
- Automotive Industry: Cutting large metal sheets to manufacture car body parts
- Construction: Cutting steel beams and structural components
- Shipbuilding: Fabricating ship components
- Metal Fabrication: Cutting machinery parts
- Recycling Industry: Processing scrap metal
8. How does the initial investment of laser cutting machines compare to hydraulic shearing machines?
The initial investment for laser cutting machines is significantly higher than that for hydraulic shearing machines. Laser cutters require advanced technology and precision engineering, leading to higher costs for purchase and setup. In contrast, hydraulic shearing machines are more affordable during the shearing process, making them a more accessible option for businesses with limited budgets or those focusing on high-speed cutting of thick metal sheets.
Conductive Cloth Tape,Double Sided Copper Tape,Conductive Metal Tape,Copper Foil Tape
Kunshan An De Qing Electric Technology Co., Ltd. , https://www.andeqing.com